Method and equipment for manufacturing separated type RFID (radiofrequency identification) tags for antennas
A technology for RFID tags and manufacturing methods, applied to antennas, antenna parts, antenna supports/installation devices, etc., can solve the problems of large antenna distance, waste of raw materials, waste of raw materials, etc., and achieve less waste discharge and lower Effects of material loss and shortened travel distance
- Summary
- Abstract
- Description
- Claims
- Application Information
AI Technical Summary
Problems solved by technology
Method used
Image
Examples
Embodiment Construction
[0039] The present invention will be described in detail below in conjunction with the embodiment of the split antenna RFID tag and the device.
[0040] figure 2 The embodiment of the split antenna RFID tag mainly includes four parts: a die-cut aluminum foil antenna 501, an RFID unit 502, a PET film 504 and a face paper 506, which are stacked sequentially from bottom to top to form a split antenna RFID tag.
[0041] Such as image 3 , the RFID unit 502 includes a base film 5021, a radiation antenna 5022 printed on the base film, and a radio frequency IC5023; the radiation antenna 5022 is generally square, and the lower side is bent inward to form an inner concave part of the middle opening, and the radio frequency IC5023 is connected to the opening place. The RFID unit 502 can be manufactured using traditional techniques, with adhesive on the back and attached to the base tape 502' with a certain step distance L2, and the base tape 502' adopts a release tape such as a relea...
PUM
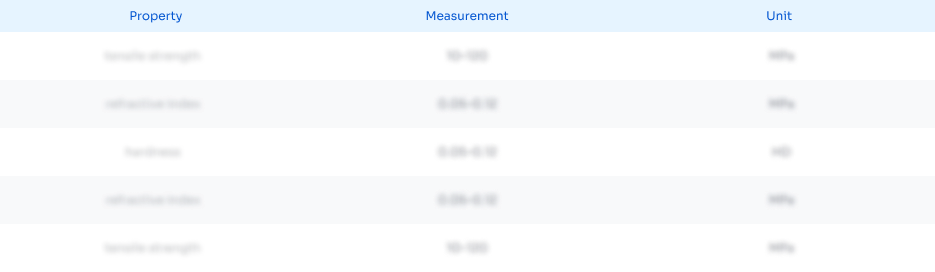
Abstract
Description
Claims
Application Information

- Generate Ideas
- Intellectual Property
- Life Sciences
- Materials
- Tech Scout
- Unparalleled Data Quality
- Higher Quality Content
- 60% Fewer Hallucinations
Browse by: Latest US Patents, China's latest patents, Technical Efficacy Thesaurus, Application Domain, Technology Topic, Popular Technical Reports.
© 2025 PatSnap. All rights reserved.Legal|Privacy policy|Modern Slavery Act Transparency Statement|Sitemap|About US| Contact US: help@patsnap.com