Ceramic ball valve high in corrosion resistance and erosive abrasion resistance
A ceramic ball valve and corrosion-resistant technology, applied in the field of ceramic ball valves, can solve the problems of valve wear, leakage and scratches in the multi-phase flow conveying system, achieve good comprehensive performance, wide application prospects, and ensure the effect of sealing
- Summary
- Abstract
- Description
- Claims
- Application Information
AI Technical Summary
Problems solved by technology
Method used
Image
Examples
Embodiment Construction
[0014] The present invention will be further described below in conjunction with drawings and embodiments.
[0015] Such as figure 1 , figure 2 As shown, the present invention includes two valve bodies 1, valve seat 2, rebound gasket 3, valve cover 4, packing gland 5, valve stem 6, actuator 7, graphite packing 8, O-ring 9 with the same structure and the bow-shaped notch valve ball 10; the two valve bodies 1 and the valve cover 4 are connected and fixed by bolts, and are sealed by O-rings 9; the inner centers of the two valve bodies 1 are respectively equipped with detachable stepped valve seats 2, and the stepped The outer shoulder of the shaped valve seat 2 and the inner side of the valve body 1 are fixed by the rebound gasket 3, and the inner side of the valve seat 2 forms a surface contact seal with the bow-shaped notch valve ball 10; the valve stem 6 is embedded in the circumferential gap connecting the valve cover 4 Graphite filler 8, and fixed by bolts through the pac...
PUM
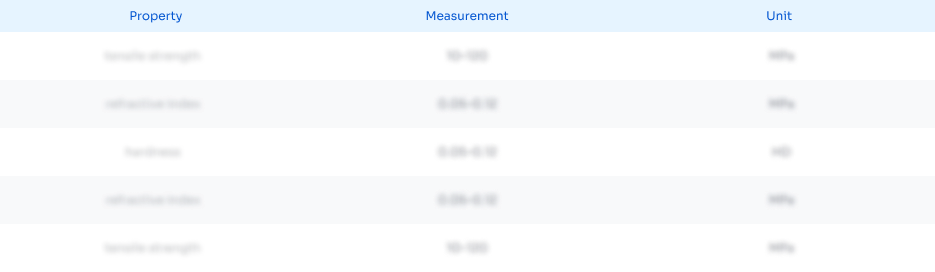
Abstract
Description
Claims
Application Information

- R&D Engineer
- R&D Manager
- IP Professional
- Industry Leading Data Capabilities
- Powerful AI technology
- Patent DNA Extraction
Browse by: Latest US Patents, China's latest patents, Technical Efficacy Thesaurus, Application Domain, Technology Topic, Popular Technical Reports.
© 2024 PatSnap. All rights reserved.Legal|Privacy policy|Modern Slavery Act Transparency Statement|Sitemap|About US| Contact US: help@patsnap.com