A method of calcification-carbonization processing of low-grade aluminum-containing raw materials and aluminum circulation
A low-grade, carbonization technology, applied in the field of comprehensive utilization of resources, can solve the problems of increasing production process costs, adverse effects, and high energy consumption, and achieve the effects of improving environmental protection standards, low production energy consumption, and reducing the amount of CO2 gas
- Summary
- Abstract
- Description
- Claims
- Application Information
AI Technical Summary
Problems solved by technology
Method used
Image
Examples
Embodiment 1
[0041] Crush the bauxite to -250μm, mix the calcium aluminate and bauxite at a mass ratio of 1.2:1, and react with calcification transformation in the 1# dissolution solution for 90 minutes at a temperature of 280°C, and the sodium oxide in the 1# dissolution solution The concentration is 280g / L, the molar ratio of sodium oxide to alumina is 3.5:1, and the pulp produced during the calcification transformation dissolution process is diluted and solid-liquid separated to obtain calcified slag with hydrated garnet as the main phase and 1# dissolution mother liquor, 1 #The molar ratio of sodium oxide to aluminum oxide in the dissolution mother liquor is reduced to 1.6:1. After the 1# dissolution mother liquor is refined with lime milk and added with aluminum hydroxide seed crystals to decompose and precipitate aluminum hydroxide, the molar ratio of sodium oxide to alumina is 3.5: The 1# decomposed mother liquor of 1, the 1# decomposed mother liquor is evaporated and the concentrati...
Embodiment 2
[0047] Crush the bauxite to -250μm, mix the calcium aluminate and bauxite at a mass ratio of 0.5:1, and perform the calcification transformation dissolution reaction in the 1# dissolution solution at a temperature of 130°C for 15 minutes, and oxidize in the 1# dissolution solution The sodium concentration is 100g / L, and the molar ratio of sodium oxide to alumina is 2.5:1. The pulp produced during the calcification transformation dissolution process is diluted and solid-liquid separated to obtain calcified slag with hydrated garnet as the main phase and 1# dissolution mother liquor. 1# dissolves Na in the mother liquor 2 The molar ratio of O and alumina is reduced to 1.7:1, and the 1# dissolution mother liquor is refined by lime milk and decomposed by adding aluminum hydroxide seed crystals, and after aluminum hydroxide is precipitated, 1# decomposition with a molar ratio of sodium oxide to alumina of 2.5:1 is obtained. Mother liquor, the 1# decomposed mother liquor is evaporat...
Embodiment 3
[0053] Crush the bauxite to -250μm, mix calcium aluminate and bauxite at a mass ratio of 0.7:1, and calcify in 1# dissolution mother liquor at a temperature of 240°C for 60min. The concentration of sodium oxide in 1# dissolution mother liquor is 100g / L, the molar ratio of sodium oxide to alumina is 2.5:1, the pulp produced in the dissolution process of calcification transformation is diluted and separated from solid and liquid to obtain calcified slag with hydrated garnet as the main phase and 1# dissolution mother liquor, which is transformed through calcification After 1# dissolves Na in the mother liquor 2 The molar ratio of O and alumina is reduced to 1.55:1, and the 1# dissolution mother liquor is refined by lime milk and decomposed by adding aluminum hydroxide seed crystals, and aluminum hydroxide is precipitated to obtain 1# decomposition with a molar ratio of sodium oxide to alumina of 2.5:1. Mother liquor, the 1# decomposed mother liquor is evaporated and the concentr...
PUM
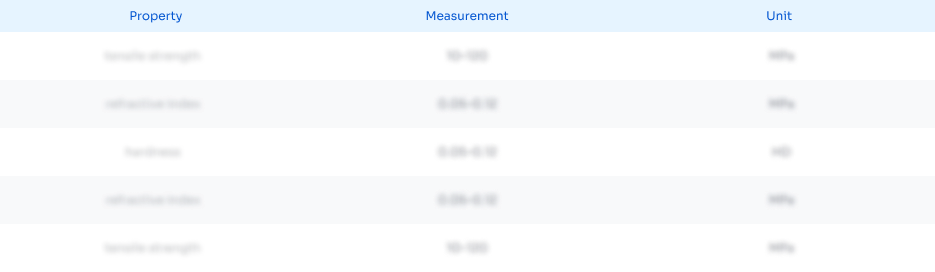
Abstract
Description
Claims
Application Information

- R&D Engineer
- R&D Manager
- IP Professional
- Industry Leading Data Capabilities
- Powerful AI technology
- Patent DNA Extraction
Browse by: Latest US Patents, China's latest patents, Technical Efficacy Thesaurus, Application Domain, Technology Topic, Popular Technical Reports.
© 2024 PatSnap. All rights reserved.Legal|Privacy policy|Modern Slavery Act Transparency Statement|Sitemap|About US| Contact US: help@patsnap.com