Method for preparing feed grade calcium hydrogen phosphate co-production water glass by using slag acid and yellow phosphorus slag
A technology for yellow phosphorus slag and calcium hydrogen phosphate, which is applied in the field of preparing feed-grade calcium hydrogen phosphate co-production water glass, can solve the problems of lower quality of calcium phosphate rock, high process cost, and difficulty in industrialization, and reduce the cost of pharmaceuticals. Effect
- Summary
- Abstract
- Description
- Claims
- Application Information
AI Technical Summary
Problems solved by technology
Method used
Image
Examples
Embodiment 1
[0026] Example 1 Under normal temperature conditions, leaching 25g of yellow phosphorus slag with 100g of slag acid from the phosphoric acid industry as raw material, stirring for 0.5h at a stirring speed of 200 rpm. After crystallization, the feed grade calcium hydrogen phosphate is precipitated, and the feed grade calcium hydrogen phosphate meets the requirements of the national standard GB / T22549-2008. After adding 30% sodium hydroxide solution to the filtrate containing silicic acid and impurities, the reaction temperature is 70°C and the reaction time is After 35 minutes, the mass concentration of NaOH at the end of the reaction was 3.4 g / L. The reacted water glass is used as the inhibitor of phosphate rock flotation, and the collector is added, and the index of the phosphate concentrate after positive and negative flotation is P 2 o 5 28.92%; MgO0.68%; Fe 2 o 3 1.92%;Al 2 o 3 1.50%. Meet the raw material requirements for the production of wet-process phosphoric a...
Embodiment 2
[0027] Example 2 Under normal temperature conditions, leaching 38g of yellow phosphorus slag with 100g of slag acid from the phosphoric acid industry as a raw material, stirring for 1.5h at a stirring speed of 240 rpm. After crystallization, the feed grade calcium hydrogen phosphate is precipitated, and the feed grade calcium hydrogen phosphate meets the requirements of the national standard GB / T22549-2008. After adding 42% sodium hydroxide solution to the filtrate containing silicic acid and impurities, the reaction temperature is 80°C and the reaction time is After 55 minutes, the mass concentration of NaOH at the end of the reaction was 4.3 g / L. The reacted water glass is used as the inhibitor of phosphate rock flotation, and the collector is added, and the index of the phosphate concentrate after positive and negative flotation is P 2 o 5 28.71%; MgO0.74%; Fe 2 o 3 1.80%;Al 2 o 3 1.64%. Meet the raw material requirements for the production of wet-process phosphoric...
Embodiment 3
[0028] Example 3 Under normal temperature conditions, leaching 32g of yellow phosphorus slag with 100g of slag acid from the phosphoric acid industry as raw material, stirring for 1.0h at a stirring speed of 300 rpm. After crystallization, the feed grade calcium hydrogen phosphate is precipitated, and the feed grade calcium hydrogen phosphate meets the requirements of the national standard GB / T22549-2008. After adding 36% sodium hydroxide solution to the filtrate containing silicic acid and impurities, the reaction temperature is 95°C and the reaction time is After 40 minutes, the mass concentration of NaOH at the end of the reaction was 2.9 g / L. The reacted water glass is used as the inhibitor of phosphate rock flotation, and the collector is added, and the index of the phosphate concentrate after positive and negative flotation is P 2 o 5 28.85%; MgO0.71%; Fe 2 o 3 1.69%;Al 2 o 3 1.80%. Meet the raw material requirements for the production of wet-process phosphoric aci...
PUM
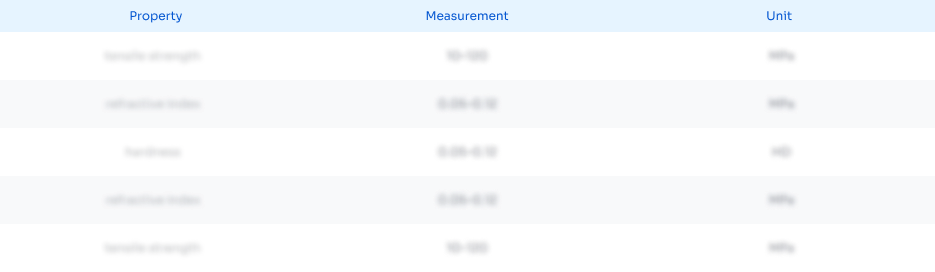
Abstract
Description
Claims
Application Information

- R&D
- Intellectual Property
- Life Sciences
- Materials
- Tech Scout
- Unparalleled Data Quality
- Higher Quality Content
- 60% Fewer Hallucinations
Browse by: Latest US Patents, China's latest patents, Technical Efficacy Thesaurus, Application Domain, Technology Topic, Popular Technical Reports.
© 2025 PatSnap. All rights reserved.Legal|Privacy policy|Modern Slavery Act Transparency Statement|Sitemap|About US| Contact US: help@patsnap.com