A system and process for defoaming and recycling
A recirculation and defoaming technology, applied in the filtration circuit, foam dispersion/prevention, filtration separation, etc., can solve the problems of accelerating the bubble escape rate, affecting the physical and chemical properties of liquid materials, and not suitable for continuous operation
- Summary
- Abstract
- Description
- Claims
- Application Information
AI Technical Summary
Problems solved by technology
Method used
Image
Examples
Embodiment 1
[0022]The new liquid material enters the stirring tank under the action of the vacuum pump and the suction pipe for uniform speed and constant temperature stirring. The stirred liquid material is sent into the first vacuum defoaming tank through the metal pipeline under the action of vacuum suction. The first degassing treatment is carried out, and the liquid material after the first degassing is sent to the second waterfall degassing tank through the metal pipeline under the action of vacuum suction for the second degassing treatment, and the liquid material after the second degassing is vacuum After being filtered by the first filter under the action of suction, it is sent to the third vacuum degassing tank for three times of degassing treatment, and the liquid material after three times of degassing enters the storage tank under the action of vacuum suction, and then filtered through the second filter After the disc spin coating operation, the remaining liquid material flows...
Embodiment 2
[0024] The degassing and recycling process of embodiment 2 is the same as that of embodiment 1, and the process parameter conditions of the agitated tank are: the temperature in the tank is 40° C., and the rotational speed of the agitator is 30 rpm; the process parameter conditions of the first vacuum degassing tank are: ultrasonic vibration frequency It is 60Hz, the vacuum degree is -90Kp, and the degassing time is 90 minutes; the process parameter condition of the second waterfall type degassing tank is: the degassing time is 70 minutes; the process parameter condition of the third vacuum degassing tank is: the vacuum degree is - 90Kp. The liquid material is degassed under the conditions of the above process parameters, the air bubble rate is 0.1% per thousand discs after spin coating, and the diameter of the bubbles on the disc surface is less than 40 μm.
Embodiment 3
[0026] The degassing and recycling process of embodiment 3 is the same as that of embodiment 1. The process parameter conditions of the agitated tank are: the temperature in the tank is 44° C., and the rotational speed of the agitator is 40 rpm; the process parameter conditions of the first vacuum degassing tank are: ultrasonic vibration frequency It is 70Hz, the vacuum degree is -100Kp, and the degassing time is 70 minutes; the process parameter condition of the second waterfall type degassing tank is: the degassing time is 90 minutes; the process parameter condition of the third vacuum degassing tank is: the vacuum degree is - 100Kp. The liquid material is degassed under the conditions of the above process parameters, the air bubble rate is 0.1% per thousand discs after spin coating, and the diameter of the bubbles on the disc surface is less than 40 μm.
PUM
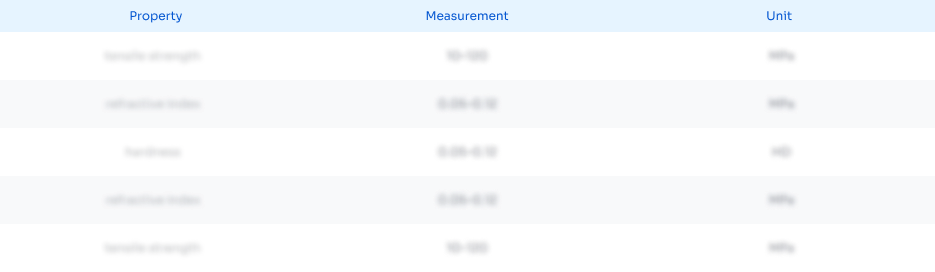
Abstract
Description
Claims
Application Information

- R&D
- Intellectual Property
- Life Sciences
- Materials
- Tech Scout
- Unparalleled Data Quality
- Higher Quality Content
- 60% Fewer Hallucinations
Browse by: Latest US Patents, China's latest patents, Technical Efficacy Thesaurus, Application Domain, Technology Topic, Popular Technical Reports.
© 2025 PatSnap. All rights reserved.Legal|Privacy policy|Modern Slavery Act Transparency Statement|Sitemap|About US| Contact US: help@patsnap.com