Printing and dyeing process of cotton fabric
A printing and dyeing process, cotton fabric technology, applied in the field of textile production, can solve the problems of endangering the environment and human health, non-degradable printing and dyeing auxiliaries, difficult to handle waste liquid, etc., achieve rapid dyeing, reduce procedures, and improve the cycle of the process.
- Summary
- Abstract
- Description
- Claims
- Application Information
AI Technical Summary
Problems solved by technology
Method used
Examples
Embodiment 1
[0025] Prepare a pretreatment solution with the following components:
[0026] Cellulase 0.5g / l, pectinase 6g / l, protease 0.5g / l, HAc 1g / l, NaAc 0.5g / l, hydrogen peroxide 25g / l, chelating dispersant 1g / l, nonanoyloxybenzenesulfonic acid Sodium 1.2g / l;
[0027] Immerse the fabric in the pretreatment tank, control the bath ratio in the pretreatment tank to 1:4, start the ultrasonic generator set on the pretreatment tank, emit 40kHz ultrasonic waves, and pad at 40°C for 35min;
[0028] Prepare a staining solution with the following components:
[0029] Dye 20g / L, N-methylol acrylamide 5g / L, α-olefin sulfonate 2g / L, Methylene diphenyl ether disulfonate 8g / L, polyquaternary ammonium fixing agent 2g / L, Water glass 5g / L, dimethyldihydroxycycloethylene urea resin 5g / L, isopropanol 0.65g / L, sodium naphthalene vinyl sulfate 0.25g / L, diethylenetriaminepentaacetic acid 0.35g / L, Wet rubbing fastness improving agent DM-258 is 10g / L, finishing agent 1g / L, antibacterial agent 7g / L;
[003...
Embodiment 2
[0035] Prepare a pretreatment solution with the following components:
[0036] Cellulase 2g / L, pectinase 4g / L, protease 0.8g / L, HAc 0.1g / L, NaAc 2g / L, hydrogen peroxide 20g / L, chelating dispersant 1.5g / L, nonanoyloxybenzenesulfonic acid Sodium 1g / L;
[0037] Immerse the fabric in the pre-treatment tank, control the bath ratio in the pre-treatment tank to 1:5, start the ultrasonic generator set on the pre-treatment tank, emit 40 kHz ultrasonic waves, and pad at 35 ° C for 40 minutes;
[0038] Prepare a staining solution with the following components:
[0039] Dye 15g / L, N-methylol acrylamide 8g / L, α-olefin sulfonate 5g / L, Methylene diphenyl ether disulfonate 5g / L, polyquaternary ammonium fixing agent 5g / L , water glass 10g / L, dimethyl dihydroxycycloethylene urea resin 2g / L, isopropanol 0.85g / L, sodium naphthalene vinyl sulfate 0.05g / L, diethylenetriaminepentaacetic acid 0.55g / L , Wet rubbing fastness improving agent DM-258 is 8g / L, finishing agent 5g / L, antibacterial agent 5...
Embodiment 3
[0045] Prepare a pretreatment solution with the following components:
[0046] The treatment solution contains cellulase 1g / L, pectinase 5g / L, protease 0.6g / L, HAc0.5g / L, NaAc1g / L, hydrogen peroxide 22g / L, chelating dispersant 1.2g / L, nonanoyl oxygen Sodium phenyl sulfonate 1g / L;
[0047] Immerse the fabric in the pretreatment tank, control the bath ratio in the pretreatment tank to 1:4.5, start the ultrasonic generator set on the pretreatment tank, emit 40kHz ultrasonic waves, and pad at 35°C for 35 minutes;
[0048] Prepare a staining solution with the following components:
[0049] Dye 18g / L, N-methylolacrylamide 7g / L, α-olefin sulfonate 3g / L, methylene diphenyl ether disulfonate 6g / L, polyquaternary ammonium color-fixing agent 4g / L, Water glass 8g / L, dimethyldihydroxycycloethylene urea resin 3g / L, isopropanol 0.7g / L, sodium naphthalene ethylene sulfate 0.2g / L, diethylenetriaminepentaacetic acid 0.4g / L, The wet rubbing fastness enhancer DM-258 is 9g / L, the finishing agen...
PUM
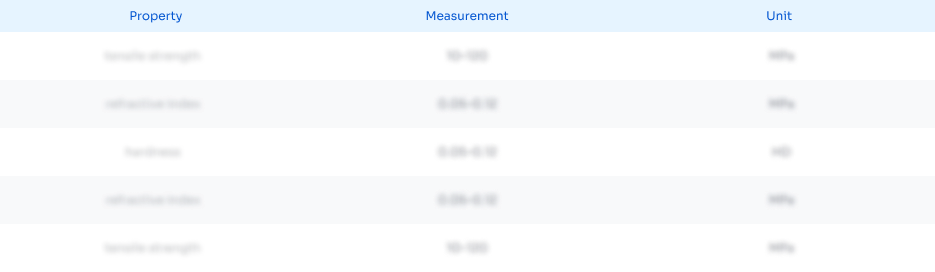
Abstract
Description
Claims
Application Information

- Generate Ideas
- Intellectual Property
- Life Sciences
- Materials
- Tech Scout
- Unparalleled Data Quality
- Higher Quality Content
- 60% Fewer Hallucinations
Browse by: Latest US Patents, China's latest patents, Technical Efficacy Thesaurus, Application Domain, Technology Topic, Popular Technical Reports.
© 2025 PatSnap. All rights reserved.Legal|Privacy policy|Modern Slavery Act Transparency Statement|Sitemap|About US| Contact US: help@patsnap.com