High-performance polyurethane elastomer and preparation method thereof
A polyurethane elastomer, high-performance technology, applied in the field of high-performance polyurethane elastomer and its preparation, can solve the problems of environmental pollution, deterioration of prepolymer, physical injury of operators, etc., and achieves high bearing performance, low dynamic heat generation, The effect of reducing environmental pollution
- Summary
- Abstract
- Description
- Claims
- Application Information
AI Technical Summary
Problems solved by technology
Method used
Image
Examples
Embodiment 1
[0031] (1) Preparation of component A: Dehydrate 400g of PCL with a number average molecular weight of 2000 at 95-100°C for 2h at a vacuum degree of -0.1MPa, add 67.6g of PPDI, react at 70-80°C for 1.5h, and vacuum dehydrate Soak and set aside.
[0032] (2) Preparation of component B: After melting 100g of HER at 85°C, mix it with 0.4g of catalyst (a solution with 33% triethylenediamine content prepared in propylene glycol) and keep it in a liquid state.
[0033] (3) Preparation of elastomer: Keep component A at 75-80°C, component B at 80-85°C, mix A / B components uniformly according to the weight ratio of 100 / 9 and defoam, pour 120 In the mold at ℃, demould for 60 minutes, vulcanize for 20 hours at 120 ℃, and measure performance after 7 days at room temperature. The properties of the obtained materials are shown in Table 2.
Embodiment 2
[0035] (1) Preparation of component A: Dehydrate 400g of PCL with a number average molecular weight of 1000 at 95-100°C for 2h at a vacuum of -0.1MPa, add 118g of PPDI, react at 70-80°C for 1.5h, and vacuum defoam , the material is ready for use.
[0036] (2) Preparation of component B: Melt 60g of HER and 30g of HQEE at 100°C, mix with 0.45g of catalyst (a solution with 33% triethylenediamine content prepared in propylene glycol) and keep it in a liquid state .
[0037] (3) Preparation of elastomer: Keep component A at 75-80°C, component B at 85-90°C, mix A / B components uniformly according to the weight ratio of 100 / 12 and defoam, pour 120 In the mold at ℃, demould for 30 minutes, vulcanize for 20 hours at 120 ℃, and measure performance after 7 days at room temperature. The properties of the obtained materials are shown in Table 2.
Embodiment 3
[0039] (1) Preparation of component A: Dehydrate 400g of PCL with a number-average molecular weight of 1000 at 95-100°C for 2h at a vacuum of -0.1MPa, add 104.5g of PPDI, and react at a temperature of 70-80°C for 1.5h , vacuum defoaming, and discharge for later use.
[0040](2) Preparation of component B: After melting 50g of HER, 50g of HQEE and 15.7g of TIPA at 100°C, they were evenly mixed with 0.4g of T12 catalyst and kept in a liquid state.
[0041] (3) Preparation of elastomer: Keep component A at 75-80°C, component B at 85-90°C, mix A / B components uniformly according to the weight ratio of 100 / 8.3 and defoam, pour 120 In the mold at ℃, demould for 60 minutes, vulcanize for 20 hours at 120 ℃, and measure performance after 7 days at room temperature. The properties of the obtained materials are shown in Table 2.
PUM
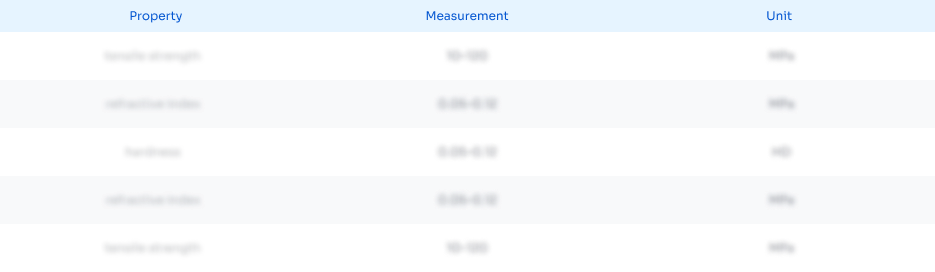
Abstract
Description
Claims
Application Information

- Generate Ideas
- Intellectual Property
- Life Sciences
- Materials
- Tech Scout
- Unparalleled Data Quality
- Higher Quality Content
- 60% Fewer Hallucinations
Browse by: Latest US Patents, China's latest patents, Technical Efficacy Thesaurus, Application Domain, Technology Topic, Popular Technical Reports.
© 2025 PatSnap. All rights reserved.Legal|Privacy policy|Modern Slavery Act Transparency Statement|Sitemap|About US| Contact US: help@patsnap.com