Novel linear rolling and sliding composite guide rail pair
A guide rail pair and straight line technology, applied in the field of guide rail pairs, can solve problems such as difficulty in meeting performance indicators and precision requirements of heavy-duty machine tools, large contact area of sliding guide rails, poor vibration resistance, poor rigidity, etc., and achieve excellent manufacturing process and good motion performance , the effect of large carrying capacity
- Summary
- Abstract
- Description
- Claims
- Application Information
AI Technical Summary
Problems solved by technology
Method used
Image
Examples
Embodiment 1
[0028] A new type of linear rolling-sliding composite guide rail pair of the present invention comprises a guide rail 4 and a slider 1 that cooperate with each other, the guide rail 4 is a trapezoidal guide rail, the two sides of the trapezoidal guide rail are guide surfaces 3a, and the upper surface of the trapezoidal guide rail is bearing surface 2a,
[0029] A trapezoidal groove matching the trapezoidal guide rail is provided at the bottom of the slider 4, and a row of cylindrical roller rows 2 are respectively arranged on the two sides of the trapezoidal groove along the length direction, and the upper surface 1a of the trapezoidal groove of the slider 4 and the load bearing The flexible belt 3 of the guide rail is arranged along the length direction of the guide rail 4 between the surfaces 2a.
[0030] The material of the guide rail 4, the cylindrical roller and the slide block 1 is steel. Both the guide surface 3a and the bearing surface 2a of the guide rail are quenche...
Embodiment 2
[0033] A new type of linear rolling-sliding composite guide rail pair of the present invention comprises a guide rail 4 and a slider 1 that cooperate with each other, the guide rail 4 is a trapezoidal guide rail, the two sides of the trapezoidal guide rail are guide surfaces 3a, and the upper surface of the trapezoidal guide rail is Bearing surface 2a.
[0034] The bottom of the slider 4 is provided with a trapezoidal groove matching the trapezoidal guide rail. Two rows of cylindrical roller columns 2 are respectively arranged on the two sides of the trapezoidal groove along the length direction. The upper surface 1a of the trapezoidal groove of the slider 4 and the load bearing The flexible belt 3 of the guide rail is arranged along the length direction of the guide rail 4 between the surfaces 2a.
[0035] The material of the guide rail 4, the cylindrical roller and the slide block 1 is steel. Both the guide surface 3a and the bearing surface 2a of the guide rail are quenche...
PUM
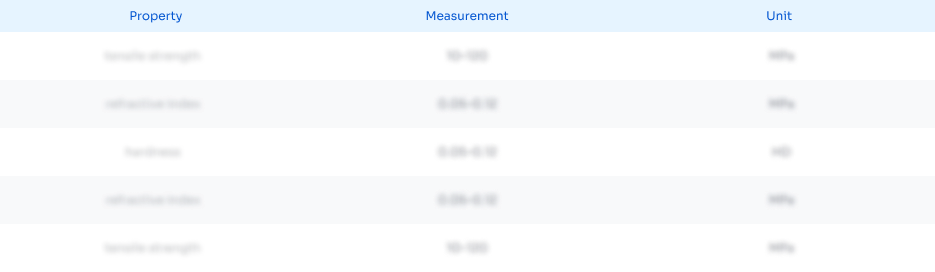
Abstract
Description
Claims
Application Information

- R&D
- Intellectual Property
- Life Sciences
- Materials
- Tech Scout
- Unparalleled Data Quality
- Higher Quality Content
- 60% Fewer Hallucinations
Browse by: Latest US Patents, China's latest patents, Technical Efficacy Thesaurus, Application Domain, Technology Topic, Popular Technical Reports.
© 2025 PatSnap. All rights reserved.Legal|Privacy policy|Modern Slavery Act Transparency Statement|Sitemap|About US| Contact US: help@patsnap.com