Rotor sheet for motor
A technology for punching rotors and rotors, which is applied in the field of rotor punching for motors. It can solve the problems of reducing motor efficiency, damage to dies, and increasing aluminum costs, and achieves the effects of reducing mold costs, ensuring product quality, and prolonging service life.
- Summary
- Abstract
- Description
- Claims
- Application Information
AI Technical Summary
Problems solved by technology
Method used
Image
Examples
Embodiment
[0013] Such as figure 1 As shown, a rotor stamping for a motor includes a rotor stamping body 1, on which the rotor stamping body 1 is provided with rotor stamping grooves 2 uniformly distributed along its circumference, and the rotor stamping grooves 2 are punched along the The radial extension of the sheet body is 50 pieces, and the rotor punching groove 2 is a closed groove.
[0014] The distance between the outer end of the rotor punching groove and the outer edge of the rotor punching sheet is 1mm.
[0015] After the motor rotor punching plate adopts the closed groove shape, there is no need for a middle sleeve in the cast aluminum mold, which reduces the cost of the mold, improves the production efficiency, and ensures the product quality. When the cast aluminum rotor is processed, it will not cause built-up edge residue, reduce the stray loss of the motor, and improve the efficiency of the motor.
PUM
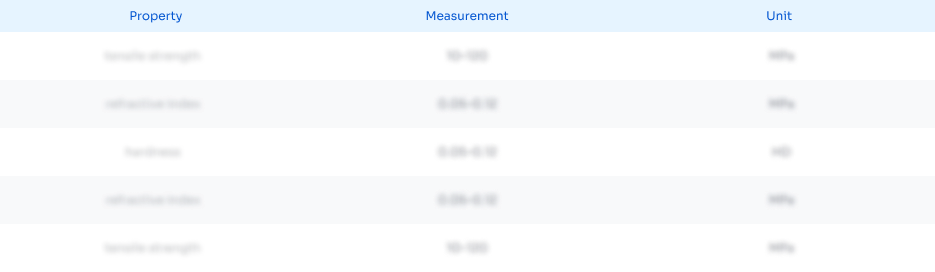
Abstract
Description
Claims
Application Information

- R&D
- Intellectual Property
- Life Sciences
- Materials
- Tech Scout
- Unparalleled Data Quality
- Higher Quality Content
- 60% Fewer Hallucinations
Browse by: Latest US Patents, China's latest patents, Technical Efficacy Thesaurus, Application Domain, Technology Topic, Popular Technical Reports.
© 2025 PatSnap. All rights reserved.Legal|Privacy policy|Modern Slavery Act Transparency Statement|Sitemap|About US| Contact US: help@patsnap.com