Temperature control method for equipment on satellite in system level thermal vacuum test
A temperature control method and thermal vacuum test technology, applied in the direction of temperature control using electric methods, can solve problems such as under-testing, high spacecraft temperature, failure to meet the purpose of assessment, etc., to improve the temperature change rate and ensure safety , Reduce the effect of excessive loading current
- Summary
- Abstract
- Description
- Claims
- Application Information
AI Technical Summary
Problems solved by technology
Method used
Image
Examples
Embodiment Construction
[0031] Below in conjunction with accompanying drawing and specific embodiment the present invention is described in further detail:
[0032] Such as figure 1 Shown is the work flow diagram of the temperature control method for the on-board equipment of the system-level thermal vacuum test of the present invention, and the temperature control method of the on-board equipment of the system-level thermal vacuum test of the present invention includes the following steps:
[0033] The first is the test preparation stage, including the following steps:
[0034] Step (1), first of all, collect relevant data, such as figure 2 Shown is a schematic diagram of the input and output of the collection of relevant documents and data of the present invention. The relevant data to be collected mainly include the technical requirements of the thermal balance test for the test tooling (including the infrared cage), the thermal balance test outline, the whole star thermal analysis / thermal desig...
PUM
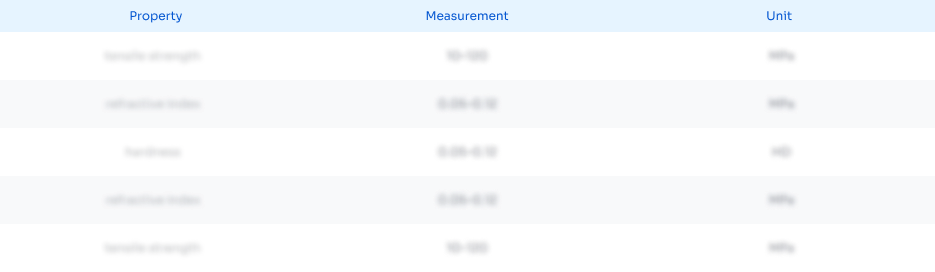
Abstract
Description
Claims
Application Information

- R&D
- Intellectual Property
- Life Sciences
- Materials
- Tech Scout
- Unparalleled Data Quality
- Higher Quality Content
- 60% Fewer Hallucinations
Browse by: Latest US Patents, China's latest patents, Technical Efficacy Thesaurus, Application Domain, Technology Topic, Popular Technical Reports.
© 2025 PatSnap. All rights reserved.Legal|Privacy policy|Modern Slavery Act Transparency Statement|Sitemap|About US| Contact US: help@patsnap.com