Gear chamber cover manufacturing process
A technology of gear chamber cover and manufacturing process, which is applied in the direction of machines/engines, engine components, casings, etc., to achieve low operating costs, guaranteed yield, and good process flexibility
- Summary
- Abstract
- Description
- Claims
- Application Information
AI Technical Summary
Problems solved by technology
Method used
Examples
Embodiment Construction
[0017] A gear chamber cover manufacturing process manufacturing process, the manufacturing steps are as follows:
[0018] A. Install the gear chamber cover mold, and install the mold parts together;
[0019] B. Put the mold on the preheating furnace for preheating, the preheating temperature is 150-200°C;
[0020] C. Clean the outer surface of the preheated mold;
[0021] D. Brush paint on the cleaned mold surface;
[0022] E. Place the mold on the mold clamping equipment for mold clamping and fixing;
[0023] F. Inject the melted metal liquid into the mold cavity and fill it up. The pouring temperature is 400-600°C; the injection specific pressure is 50-100Mpa, the injection speed is 1-4m / s, and the injection stroke is 10-100cm ;
[0024] G. After the injection stroke, hold the pressure for 2-6 seconds;
[0025] H. After leaving the mold for 6 seconds, take out the casting;
[0026] I. Clean up the mold.
[0027] Although the specific embodiments of the present inventi...
PUM
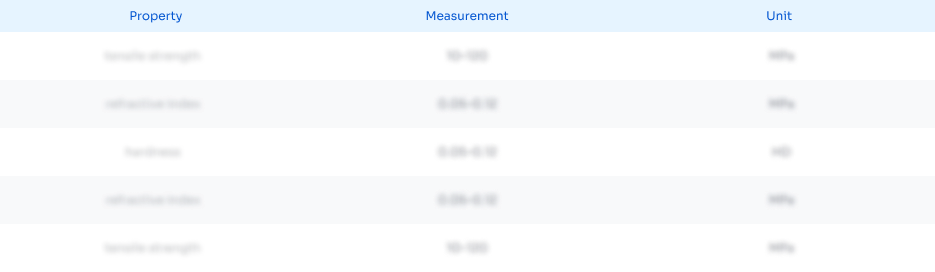
Abstract
Description
Claims
Application Information

- Generate Ideas
- Intellectual Property
- Life Sciences
- Materials
- Tech Scout
- Unparalleled Data Quality
- Higher Quality Content
- 60% Fewer Hallucinations
Browse by: Latest US Patents, China's latest patents, Technical Efficacy Thesaurus, Application Domain, Technology Topic, Popular Technical Reports.
© 2025 PatSnap. All rights reserved.Legal|Privacy policy|Modern Slavery Act Transparency Statement|Sitemap|About US| Contact US: help@patsnap.com