A sublimation transfer printing process for natural fabric or rayon
A transfer printing and fabric technology, applied in the field of textile printing, can solve the problems of environmental hazards, consumption of transfer paper, generation of sewage, etc., and achieve the effect of reducing pollution and labor intensity
- Summary
- Abstract
- Description
- Claims
- Application Information
AI Technical Summary
Problems solved by technology
Method used
Image
Examples
Embodiment 1
[0029] The mass percent composition of cloth surface treatment agent is:
[0030] Acrylic resin 20%, surfactant 2%, ethylene glycol 10%, thickener 10%, penetrant 1%, water balance;
[0031] The transfer printing process of the piece is as follows: first turn on the power of the press, adjust the embossing temperature to 220°C, the pressure to 15KG / square inch, and the time to 15s, then lay the piece flat according to the position line, and print the reconciled surface treatment agent on the piece , dry at 100°C for 2 minutes, then spread the transfer printing paper on the part of the cut piece printed with the surface treatment agent, finally press the press, wait for the press to pop up, tear off the transfer paper, and put the cut piece aside to cool can;
[0032] The printing transfer printing process is as follows: first turn on the power of the machine, adjust the embossing temperature to 220°C, the pressure to 15KG / square inch, and the time to 20s. The dry condition is...
Embodiment 2
[0034] The mass percent composition of cloth surface treatment agent is:
[0035] Acrylic resin 35%, surfactant 8%, ethylene glycol 5%, thickener 5%, penetrant 3%, water balance;
[0036] The transfer printing process of the piece is as follows: first turn on the power of the press, adjust the embossing temperature to 200°C, the pressure to 10KG / square inch, and the time to 18s, then lay the piece flat according to the position line, and print the reconciled surface treatment agent on the piece , dry at 150°C for 1 min, then spread the transfer printing paper on the part of the cut piece printed with the surface treatment agent, finally press the press, wait for the press to pop up, tear off the transfer paper, and set the cut piece aside to cool can;
[0037] The printing transfer printing process is as follows: first turn on the power of the machine, adjust the embossing temperature to 200°C, the pressure to 10KG / square inch, and the time to 18s. The drying condition is to...
Embodiment 3
[0039] The mass percent composition of cloth surface treatment agent is:
[0040] Acrylic resin 50%, surfactant 15%, ethylene glycol 0.5%, thickener 0.5%, penetrant 5%, water balance;
[0041] The transfer printing process of the cut piece is: first turn on the power of the press, adjust the embossing temperature to 180°C, the pressure to 6KG / square inch, and the time for 20s, then lay the cut piece flat according to the position line, and print the reconciled surface treatment agent on the cut piece , dry at 180°C for 30s, then spread the transfer printing paper on the part of the cut piece printed with the surface treatment agent, finally press the press, wait for the press to pop up, tear off the transfer paper, and set the cut piece aside to cool can;
[0042] The printing transfer printing process is as follows: first turn on the power of the machine, adjust the embossing temperature to 180°C, the pressure to 6KG / square inch, and the time to 20s. The drying condition is...
PUM
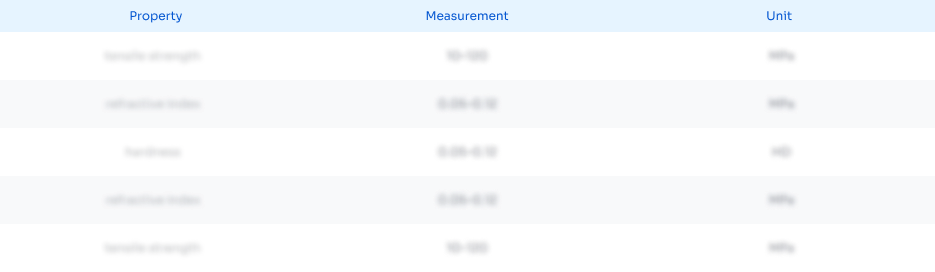
Abstract
Description
Claims
Application Information

- R&D
- Intellectual Property
- Life Sciences
- Materials
- Tech Scout
- Unparalleled Data Quality
- Higher Quality Content
- 60% Fewer Hallucinations
Browse by: Latest US Patents, China's latest patents, Technical Efficacy Thesaurus, Application Domain, Technology Topic, Popular Technical Reports.
© 2025 PatSnap. All rights reserved.Legal|Privacy policy|Modern Slavery Act Transparency Statement|Sitemap|About US| Contact US: help@patsnap.com