Small-resistance anti-stall lifting device with vertical shaft needing to move vertically
A lifting device and vertical shaft technology, applied in the direction of lifting device, lifting frame, auxiliary device, etc., can solve the problems of large moving resistance of the upper and lower shafts, no safety guarantee for stalling, and hidden safety hazards, and achieve good safety and safety. Effect
- Summary
- Abstract
- Description
- Claims
- Application Information
AI Technical Summary
Problems solved by technology
Method used
Image
Examples
Embodiment Construction
[0011] The present invention is described in detail below in conjunction with accompanying drawing and example.
[0012] See attached figure 1 , figure 2 (main view), image 3 (left view), the device is mainly composed of column components (2, 5, 10, 21, 22), ball screw drive system (1, 6, 9, 11, 20), balance system (3, 4, 7, 8 ), emergency braking system (12, 13, 14, 15, 16, 17, 18, 19,).
[0013] In the ball screw transmission system, the servo motor 1 is installed on the bracket 2, the bracket 2 is fixed on the column 5, the ball screw 6 is connected with the servo motor 1 through the coupling 11, and the ball screw 6 is equipped with The bearing realizes support, and connects the screw nut of the ball screw 6 with the moving frame 21, so that the moving frame 21 can move up and down with the rotation of the ball screw 6, and the moving frame 21 and the column 5 are connected by a guide rail slider 20 .
[0014] In the balance system, the sprocket bracket is fixed on ...
PUM
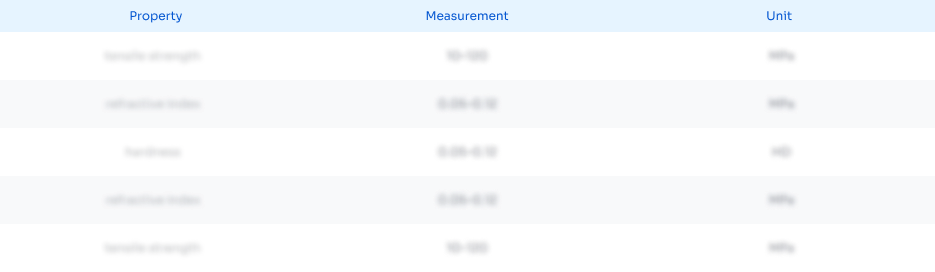
Abstract
Description
Claims
Application Information

- R&D
- Intellectual Property
- Life Sciences
- Materials
- Tech Scout
- Unparalleled Data Quality
- Higher Quality Content
- 60% Fewer Hallucinations
Browse by: Latest US Patents, China's latest patents, Technical Efficacy Thesaurus, Application Domain, Technology Topic, Popular Technical Reports.
© 2025 PatSnap. All rights reserved.Legal|Privacy policy|Modern Slavery Act Transparency Statement|Sitemap|About US| Contact US: help@patsnap.com