A kind of weaving process of wool blended fabric
A wool blending and fabric technology, applied in textiles and papermaking, knitting, weft knitting, etc., can solve the problems of poor drape and loose fabric structure, and achieve the effect of increasing voids, improving drape and tight integration
- Summary
- Abstract
- Description
- Claims
- Application Information
AI Technical Summary
Problems solved by technology
Method used
Examples
Embodiment 1
[0013] A weaving process for wool blended fabrics, comprising the following methods:
[0014] 1) Using pearl fiber as the yarn core, winding wool fiber on the pearl fiber along one direction, and then performing ultrasonic treatment, the ultrasonic power is 100W, and the treatment time is 10s;
[0015] 2) Cotton fibers are wound on the treated wool fibers in the opposite direction to obtain composite yarns, which are then woven into surface fabrics using a circular knitting machine, wherein the mass ratio of the wool fibers, cotton fibers, and pearl fibers is 100 :20:5;
[0016] 3) Coating anti-wrinkle hot melt adhesive on the surface of the surface layer fabric, the components and parts by weight of the anti-wrinkle hot melt adhesive are 30 parts of polytetramethylene ether glycol, 20 parts of butyl acrylate, and 15 parts of citrate , 12 parts of diethylene glycol diglycidyl ether, 60 parts of polyamide, 5 parts of sodium alginate, 5 parts of dioctyl phthalate;
[0017] 4) ...
Embodiment 2
[0019] A weaving process for wool blended fabrics, comprising the following methods:
[0020] 1) Use pearl fiber as the yarn core, wind wool fiber on the pearl fiber along one direction, then perform ultrasonic treatment, the ultrasonic power is 110W, and the treatment time is 15s;
[0021] 2) Cotton fibers are wound on the treated wool fibers in the opposite direction to obtain composite yarns, which are then woven into surface fabrics using a circular knitting machine, wherein the mass ratio of the wool fibers, cotton fibers, and pearl fibers is 100 :25:8;
[0022] 3) Coating anti-wrinkle hot melt adhesive on the surface of the surface layer fabric, the components and parts by weight of the anti-wrinkle hot melt adhesive are 35 parts of polytetramethylene ether glycol, 22 parts of butyl acrylate, and 16 parts of citrate , 20 parts of diethylene glycol diglycidyl ether, 55 parts of polyamide, 8 parts of sodium alginate, 6 parts of dioctyl phthalate;
[0023] 4) Use a pressi...
Embodiment 3
[0025] A weaving process for wool blended fabrics, comprising the following methods:
[0026] 1) Use pearl fiber as the yarn core, wind wool fiber on the pearl fiber along one direction, then carry out ultrasonic treatment, the ultrasonic power is 120W, and the treatment time is 20s;
[0027] 2) Cotton fibers are wound on the treated wool fibers in the opposite direction to obtain composite yarns, which are then woven into surface fabrics using a circular knitting machine, wherein the mass ratio of the wool fibers, cotton fibers, and pearl fibers is 100 :30:10;
[0028] 3) Coating anti-wrinkle hot melt adhesive on the surface of the surface layer fabric, the components and parts by weight of the anti-wrinkle hot melt adhesive are 40 parts of polytetramethylene ether glycol, 25 parts of butyl acrylate, and 18 parts of citrate , 15 parts of diethylene glycol diglycidyl ether, 50 parts of polyamide, 10 parts of sodium alginate, 8 parts of dioctyl phthalate;
[0029] 4) Use a pr...
PUM
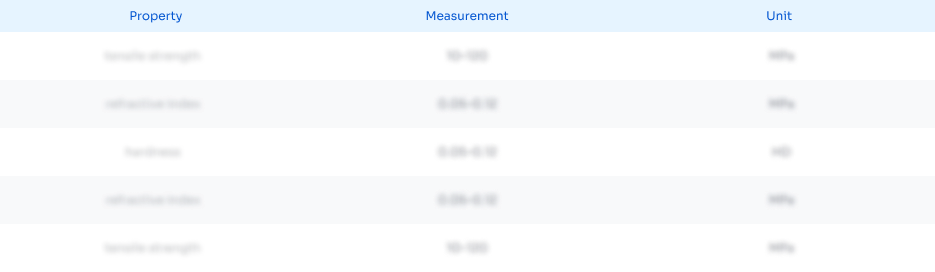
Abstract
Description
Claims
Application Information

- R&D Engineer
- R&D Manager
- IP Professional
- Industry Leading Data Capabilities
- Powerful AI technology
- Patent DNA Extraction
Browse by: Latest US Patents, China's latest patents, Technical Efficacy Thesaurus, Application Domain, Technology Topic, Popular Technical Reports.
© 2024 PatSnap. All rights reserved.Legal|Privacy policy|Modern Slavery Act Transparency Statement|Sitemap|About US| Contact US: help@patsnap.com