Process for manufacturing fiber reinforced rib-containing composite board by adopting spreading method
A composite sheet and fiber-reinforced technology, applied in the direction of manufacturing tools, chemical instruments and methods, lamination, etc., can solve the problems of unmanufacturable, high fiber requirements, complicated manufacturing process, etc., to reduce energy loss, low moisture content of raw materials, The effect of simplifying the manufacturing process
- Summary
- Abstract
- Description
- Claims
- Application Information
AI Technical Summary
Problems solved by technology
Method used
Image
Examples
Embodiment 1
[0039] see figure 1 , in an embodiment of the present invention, a process for fabricating a fiber-reinforced composite sheet with ribs by paving method includes the following steps:
[0040] (1) Stir the base material evenly in the base material mixing station 13, then put it into the primary paver 14, and spread the base material in the mobile mold to form a layer of base material layer 1;
[0041] (2) Stir the fabric evenly in the fabric mixing station 23, then put it into the secondary paver 24, and spread the fabric flat on the bottom material layer 1, and spread it into a layer of fabric layer 2;
[0042] (3) Then, the bottom material layer 1 and the fabric layer 2 are sent into the initial curing kiln 4 by a conveyor belt, and steam initial curing is carried out. The steam initial curing condition is: temperature 50-100 ° C, time 2-5 minutes, so that the material is initially set to It is beneficial to move when stacking, and stack the plates after leaving the kiln;
...
Embodiment 2
[0048] In an embodiment of the present invention, a process for fabricating a fiber-reinforced composite sheet with ribs using a paving method includes the following steps:
[0049] (1) Stir the base material evenly in the base material mixing station 13, then put it into the primary paver 14, and spread the base material in the mobile mold to form a layer of base material layer 1;
[0050] (2) Putting mesh ribs or strip ribs 3 made of metal or non-metallic materials on the bottom material layer;
[0051] (3) Stir the fabric evenly in the fabric mixing station 23, then put it into the secondary paver 24, and spread the fabric flat on the bottom material layer 1, and spread it into a layer of fabric layer 2;
[0052] (4) Then the bottom material layer and the fabric layer are sent to the initial curing kiln 4 by a conveyor belt for initial steam curing. The conditions for the initial steam curing are: the temperature is 50-80°C, and the time is 2-5 minutes, so that the material...
Embodiment 3
[0056] In an embodiment of the present invention, a process for fabricating a fiber-reinforced composite sheet with ribs using a paving method includes the following steps:
[0057] (1) Stir the base material evenly in the base material mixing station 13, then put it into the primary paver 14, and spread the base material in the mobile mold to form a layer of base material layer 1;
[0058] (2) Putting mesh ribs or strip ribs 3 made of metal or non-metallic materials on the bottom material layer;
[0059] (3) Repeat steps (1) and (2) multiple times;
[0060] (4) Stir the fabric evenly in the fabric mixing station 23, then put it into the secondary paver 24, and spread the fabric flat on the bottom material layer 1, and spread it into a layer of fabric layer 2;
[0061] (5) Repeat steps (2) and (4) multiple times;
[0062] (6) Then the bottom material layer and the fabric layer are sent to the initial curing kiln 4 by a conveyor belt for initial steam curing. The steam primar...
PUM
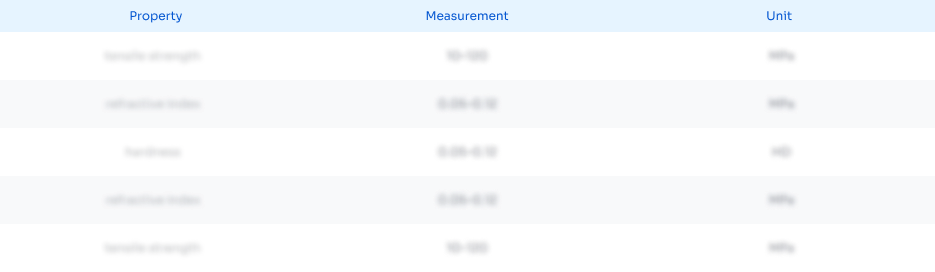
Abstract
Description
Claims
Application Information

- Generate Ideas
- Intellectual Property
- Life Sciences
- Materials
- Tech Scout
- Unparalleled Data Quality
- Higher Quality Content
- 60% Fewer Hallucinations
Browse by: Latest US Patents, China's latest patents, Technical Efficacy Thesaurus, Application Domain, Technology Topic, Popular Technical Reports.
© 2025 PatSnap. All rights reserved.Legal|Privacy policy|Modern Slavery Act Transparency Statement|Sitemap|About US| Contact US: help@patsnap.com