Fly ash raw material pellet production method
A technology for raw meal pellets and fly ash, which is applied in the field of preparation of fly ash raw meal pellets, can solve the problems of increasing sintering energy consumption and the like
- Summary
- Abstract
- Description
- Claims
- Application Information
AI Technical Summary
Problems solved by technology
Method used
Image
Examples
Embodiment Construction
[0037] The present invention is specifically described below in conjunction with accompanying drawing, as figure 1 As shown, the mixed raw material of fly ash and ammonium sulfate is sent to the raw material bin 2 by the conveyor one 1 for storage. The raw material in the raw material bin 2 enters the second conveyor 4, and is transported into the ball pressing machine 5 by the second conveyor 4. In the briquetting machine 5, the raw meal is pressed into raw meal pellets. The pellets pressed by the ball pressing machine 5 enter the belt conveyor 6, and are sent to the sieve 7 by the belt conveyor 6. The complete pellets on the sieve 7 are sent to the conveyor sintering kiln system by the conveyor 3 10, and the broken pellets screened out by the sieve 7 enter the broken ball bin 3 through the conveyor 4 8 and the conveyor 5 9 for storage. The crushed balls in the crushed ball bin 3 enter the second conveyor 4, and are mixed with the raw meal in the second conveyor 4, and fina...
PUM
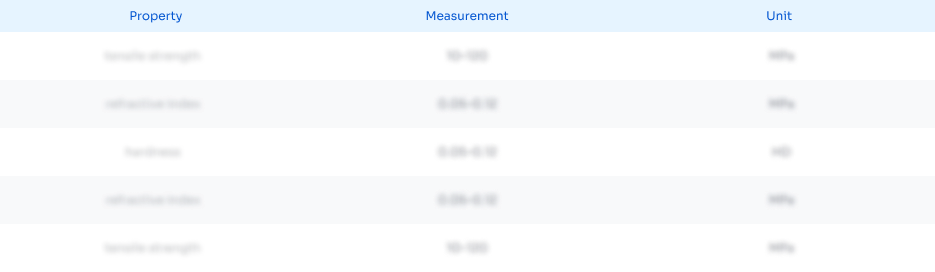
Abstract
Description
Claims
Application Information

- R&D Engineer
- R&D Manager
- IP Professional
- Industry Leading Data Capabilities
- Powerful AI technology
- Patent DNA Extraction
Browse by: Latest US Patents, China's latest patents, Technical Efficacy Thesaurus, Application Domain, Technology Topic, Popular Technical Reports.
© 2024 PatSnap. All rights reserved.Legal|Privacy policy|Modern Slavery Act Transparency Statement|Sitemap|About US| Contact US: help@patsnap.com