Thermal de-polymerization process of plastic waste materials
A waste and plastic technology, applied in the field of catalytic thermal depolymerization, can solve the problems of high maintenance cost and expensive technology
- Summary
- Abstract
- Description
- Claims
- Application Information
AI Technical Summary
Problems solved by technology
Method used
Image
Examples
Embodiment Construction
[0014] The purpose, construction, features and functions of the present invention can be better understood with reference to the detailed embodiments given below.
[0015] The invention relates to a process (100) for thermal depolymerization of waste materials, especially plastic waste (10), into liquid transport fuels (15) by using limestone (20) as a catalyst. Waste plastics (10) according to the present invention are municipal and / or industrial wastes, including but not limited to polyethylene, polypropylene and polyvinyl chloride.
[0016] In one embodiment of the present invention, the limestone catalyst (20) is obtained by sintering the following solid composition, which contains: 39% to 41% alumina (Al 2 o 3 ); 30% to 32% calcium oxide (CaO); 0.09% to 0.12% silicon monoxide (SiO); 0.01% to 0.03% magnesium oxide. Preferably, the solid composition contains 40.6% ± 0.1 alumina (Al 2 o 3 ); 31.7%±0.1 of calcium oxide (CaO); 0.15%±0.01 of silicon monoxide (SiO); and 0.03...
PUM
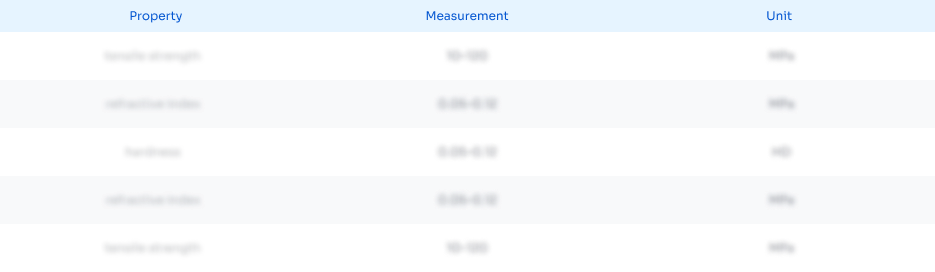
Abstract
Description
Claims
Application Information

- R&D Engineer
- R&D Manager
- IP Professional
- Industry Leading Data Capabilities
- Powerful AI technology
- Patent DNA Extraction
Browse by: Latest US Patents, China's latest patents, Technical Efficacy Thesaurus, Application Domain, Technology Topic, Popular Technical Reports.
© 2024 PatSnap. All rights reserved.Legal|Privacy policy|Modern Slavery Act Transparency Statement|Sitemap|About US| Contact US: help@patsnap.com