A Telescope Rack Control System
A technology for control systems and telescopes, applied in the field of control and electronics, to achieve good rigidity, ensure safe operation, and low noise
- Summary
- Abstract
- Description
- Claims
- Application Information
AI Technical Summary
Problems solved by technology
Method used
Image
Examples
Embodiment Construction
[0019] The principle block diagram of the rack control system is as follows: figure 1 As shown, a telescope rack control system includes a computer 2, a servo control system and a single-chip microcomputer control system, the servo control system includes a motion controller 3, and the signal input end of the motion controller 3 is connected to an azimuth axis encoder 4, a pitch axis Axis encoder 5, the signal output terminal of motion controller 3 is connected to azimuth axis driver 6 and pitch axis driver 7, and azimuth axis driver 6 and pitch axis driver 7 are connected to azimuth axis torque motor 8 and pitch axis torque motor 9 respectively; The control system includes a single-chip microcomputer 10, the signal input end of the single-chip microcomputer 10 is connected with a pitch axis speed measuring motor 11, an azimuth axis speed measuring motor 12, a pitch axis limit switch 13, an azimuth axis limit switch 14, a position sensor 15, and the signal output of the single ...
PUM
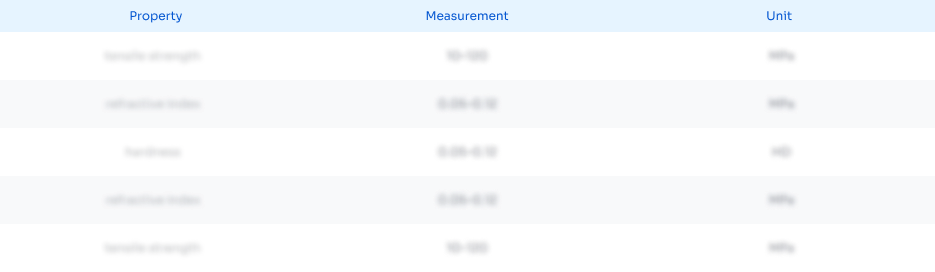
Abstract
Description
Claims
Application Information

- R&D
- Intellectual Property
- Life Sciences
- Materials
- Tech Scout
- Unparalleled Data Quality
- Higher Quality Content
- 60% Fewer Hallucinations
Browse by: Latest US Patents, China's latest patents, Technical Efficacy Thesaurus, Application Domain, Technology Topic, Popular Technical Reports.
© 2025 PatSnap. All rights reserved.Legal|Privacy policy|Modern Slavery Act Transparency Statement|Sitemap|About US| Contact US: help@patsnap.com