Texturing machine
A deformation machine, stretching deformation technology, applied in the direction of control of generators, motor generators, electromechanical brakes, etc., can solve the problems of inability to realize closed-loop control, high cost, and inability to control each processing point separately, so as to reduce the speed Monitor costs and reduce the effect of feedback bias
- Summary
- Abstract
- Description
- Claims
- Application Information
AI Technical Summary
Problems solved by technology
Method used
Image
Examples
Embodiment
[0021] Example: such as figure 1 As shown, the texturing machine includes a raw wire frame 20, a first drafting device 35, a heating device 3, a cooling device 4, a false twisting device 36, a second drafting device 37, a first conveying device 38, a second heating device 19, The second conveying device 39 and the winding device 24 . The first drafting device 35, the heating device 3, the cooling device 4, the false twisting device 36, the second drafting device 37, the first conveying device 38, the second heating device 19, and the second conveying device 39 are followed by the machine support 16 and the second conveying device 39. The main frame 40 supports. The filament is drawn out from the raw yarn bobbin 21 installed on the raw yarn rack 20, passes through the first drafting device 35, enters the first heating device 3 for heating, and the cooling device 4 cools down, and then is false twisted and deformed by the false twisting device 36, and enters the first drafting ...
PUM
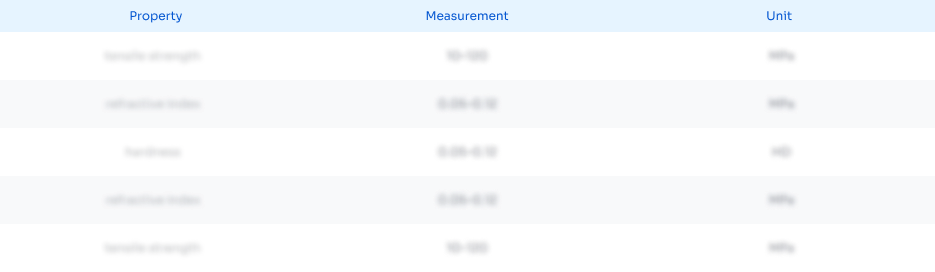
Abstract
Description
Claims
Application Information

- R&D
- Intellectual Property
- Life Sciences
- Materials
- Tech Scout
- Unparalleled Data Quality
- Higher Quality Content
- 60% Fewer Hallucinations
Browse by: Latest US Patents, China's latest patents, Technical Efficacy Thesaurus, Application Domain, Technology Topic, Popular Technical Reports.
© 2025 PatSnap. All rights reserved.Legal|Privacy policy|Modern Slavery Act Transparency Statement|Sitemap|About US| Contact US: help@patsnap.com