Micro nanocomposite material with high thermal conductivity and preparation method thereof
A composite material and micro-nano technology, applied in the field of thermally conductive composite materials, can solve the problems of high thermal conductivity, good comprehensive mechanical properties, easy agglomeration, etc., and achieve excellent thermal conductivity, enhanced mechanical properties, and easy heat conduction network.
- Summary
- Abstract
- Description
- Claims
- Application Information
AI Technical Summary
Problems solved by technology
Method used
Examples
Embodiment 1
[0024] (1) Add 1.5g of graphite to 100mL of benzylamine N,N-dimethylacetamide solution with a mass concentration of 1% under high-speed stirring, and stir at 6000rpm for 30 minutes, followed by ultrasonic stripping (ultrasonic frequency is 25KHZ, Ultrasonic power is 100W) after 1 hour, after filtering and drying, the thermally conductive filler with micro-nano structure can be obtained.
[0025] (2) Dissolve 19 g of polymethyl methacrylate (PMMA) in 100 mL of N,N-dimethylformamide under heating (50° C.) and stirring to obtain a PMMA solution.
[0026] (3) Add 1g of micro-nano structure heat-conducting filler into the PMMA solution prepared by (2) under stirring, obtain a uniformly dispersed mixed solution after stirring at a high speed of 6000rpm for 30 minutes, and slowly pour the obtained mixed solution under stirring After entering the water, the polymer mixed liquid is flocculated into a solid, and after filtering, washing 3 times, and drying, the micro-nano composite mate...
Embodiment 2
[0030] (1) Add 7.2g of expanded graphite into 120mL of N,N-dimethylformamide with a mass concentration of 3% naphthylamine under high-speed stirring, and stir at 10000rpm for 60 minutes, followed by ultrasonic stripping (ultrasonic frequency is 25KHZ, Ultrasonic power is 300W) After 8 hours, a suspension was obtained. The obtained suspension is filtered and dried to obtain the thermally conductive filler with micro-nano structure.
[0031] (2) Melting and mixing 6 g of the micro-nano structured heat-conducting filler and 14 g of polyvinyl chloride in an internal mixer to obtain a micro-nano composite material. The prepared micro-nano composite material is put into a standard mold and hot-pressed at 180° C. and 12 MPa to obtain a high thermal conductivity micro-nano composite material. The mass content of the thermally conductive filler in the composite material is 30%.
[0032] As a comparative example, a graphite-modified PVC composite (referred to as PVC‐Gn‐30) was prepare...
Embodiment 3
[0035] (1) Add 7g of expanded graphite to 350mL of naphthylamine N,N-dimethylacetamide with a mass concentration of 2% under high-speed stirring, stir at 9000rpm for 40 minutes, and then ultrasonic stripping (ultrasonic frequency is 25KHZ, ultrasonic Power is 900W) After 10 hours, a suspension was obtained. The obtained suspension is filtered and dried to obtain the thermally conductive filler with micro-nano structure.
[0036] (2) Dissolve 14g of polyvinylidene fluoride (PVDF) in 100mL of N,N-diylacetamide under heating (50°C) and stirring to obtain a PVDF solution.
[0037] (3) Add 6g of micro-nano structured filler into the PVDF solution prepared in (2), stir at 10000rpm for 40 minutes to obtain a uniformly dispersed mixed solution, slowly pour the mixed solution into water under stirring, and the polymer mixed solution flocculates into a solid , after filtering, washing with water for 3 times, and drying, the micro-nano composite material was obtained, wherein the mass c...
PUM
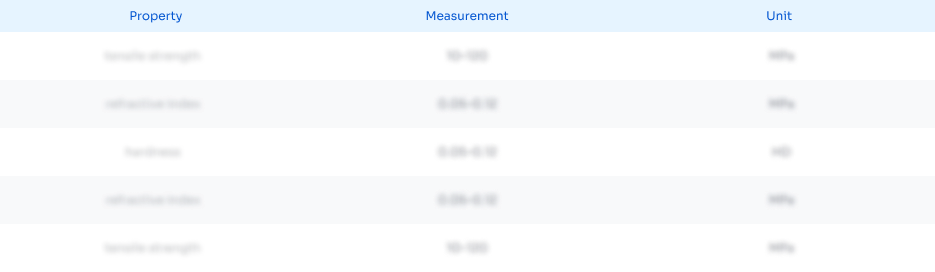
Abstract
Description
Claims
Application Information

- Generate Ideas
- Intellectual Property
- Life Sciences
- Materials
- Tech Scout
- Unparalleled Data Quality
- Higher Quality Content
- 60% Fewer Hallucinations
Browse by: Latest US Patents, China's latest patents, Technical Efficacy Thesaurus, Application Domain, Technology Topic, Popular Technical Reports.
© 2025 PatSnap. All rights reserved.Legal|Privacy policy|Modern Slavery Act Transparency Statement|Sitemap|About US| Contact US: help@patsnap.com