A thermal error prediction method for heavy machine tools considering ambient temperature
A technology of environmental temperature and prediction method, applied in computer control, program control, instrument, etc., can solve the problems of compensation accuracy failure, limited versatility, non-existence, etc., and achieve the goal of solving poor robustness and improving accuracy and robustness Effect
- Summary
- Abstract
- Description
- Claims
- Application Information
AI Technical Summary
Problems solved by technology
Method used
Image
Examples
Embodiment Construction
[0039]In order to make the object, technical solution and advantages of the present invention clearer, the present invention will be further described in detail below in conjunction with the accompanying drawings and embodiments. It should be understood that the specific embodiments described here are only used to explain the present invention, not to limit the present invention. In addition, the technical features involved in the various embodiments of the present invention described below can be combined with each other as long as they do not constitute a conflict with each other.
[0040] One, the technical thought of the present invention.
[0041] The thermal deformation error of the machine tool is decomposed into the superposition of the influence of the external environment and the internal heat source. X represents the specified thermal deformation direction to be measured, which can be the x coordinate, y coordinate and z coordinate direction in the machine tool coor...
PUM
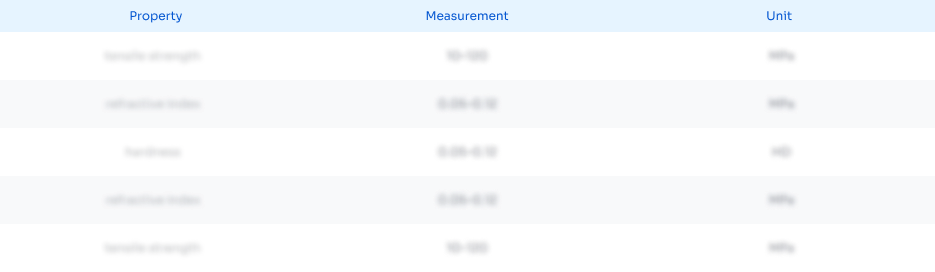
Abstract
Description
Claims
Application Information

- R&D
- Intellectual Property
- Life Sciences
- Materials
- Tech Scout
- Unparalleled Data Quality
- Higher Quality Content
- 60% Fewer Hallucinations
Browse by: Latest US Patents, China's latest patents, Technical Efficacy Thesaurus, Application Domain, Technology Topic, Popular Technical Reports.
© 2025 PatSnap. All rights reserved.Legal|Privacy policy|Modern Slavery Act Transparency Statement|Sitemap|About US| Contact US: help@patsnap.com