A method for preparing aluminum-based foam material by negative pressure foaming
An aluminum-based foam material and negative pressure technology, which is applied in the field of porous metal materials, can solve the problems of effective control of the foam aluminum expansion process, achieve the effect of saving the amount of foaming agent and improving the uniformity
- Summary
- Abstract
- Description
- Claims
- Application Information
AI Technical Summary
Problems solved by technology
Method used
Image
Examples
Embodiment 1
[0050] A method for preparing aluminum-based foam material with a target expansion rate of 315% using negative pressure foaming, the steps are as follows:
[0051] 1. Put 600g of industrial pure aluminum into a cylindrical steel crucible with a diameter of 100mm. Place the crucible in the crucible electric furnace to heat the aluminum. The temperature is kept at 740℃ and the stirring speed is 1200 rpm. Add calcium metal with a mass fraction of 2.5% aluminum to the molten aluminum, and stir for 10 minutes;
[0052] 2. Control the temperature in the furnace at 690℃, add titanium hydride with a mass fraction of aluminum 0.1% at a stirring speed of 1500 rpm, and continue stirring for 6 minutes; after the stirring stops, the expansion rate of the molten aluminum is 113%. Under continued heat preservation, the expansion rate of molten aluminum did not change significantly;
[0053] 3. Transfer the crucible to a stainless steel foaming chamber with a closed cover with a quartz observation ...
Embodiment 2
[0057] A target density of 0.65gcm prepared by negative pressure foaming -3 The method of aluminum-based foam material components, the steps are as follows:
[0058] 1. Put 700g of A356 aluminum alloy into a steel crucible and heat it in an electric furnace to melt the aluminum alloy. The temperature is kept at 740℃ and the stirring speed is 800 rpm. The mass fraction is added to the molten aluminum. Aluminum 3.0% calcium metal, stirring for 5 minutes;
[0059] 2. Control the temperature in the furnace at 710°C, add 0.4% titanium hydride with aluminum mass fraction at a stirring speed of 2000 rpm, and continue stirring for 6 minutes;
[0060] 3. Transfer the crucible to a stainless steel foaming chamber with a closed cover with a quartz observation window, use a laser rangefinder to measure the height of the melt through the quartz window, and start the air extraction device, while monitoring the pressure in the foaming chamber And the height of the foam, the pressure control range ...
Embodiment 3
[0065] A method for preparing aluminum-based foam material with a target expansion rate of 321% by using negative pressure foaming, the steps are as follows:
[0066] 1. Put 600g of industrial pure aluminum into a steel crucible, put the crucible in the crucible electric furnace to heat the aluminum, and keep the temperature at 730℃; under the condition of a stirring speed of 1000 rpm, add it to the molten aluminum. Add 1.2g of metallic magnesium as alloy component and copper-plated short carbon fiber with a volume fraction of aluminum 0.5%, and continue to stir for 4 minutes;
[0067] 2. Control the temperature in the furnace at 700℃, add calcium carbonate with a mass fraction of aluminum 0.1% at a stirring speed of 1700 rpm, and continue stirring for 8 minutes; after the stirring stops, the expansion rate of the molten aluminum is 110%. Under continued heat preservation, the expansion rate of molten aluminum did not change significantly;
[0068] 3. Transfer the crucible to a stai...
PUM
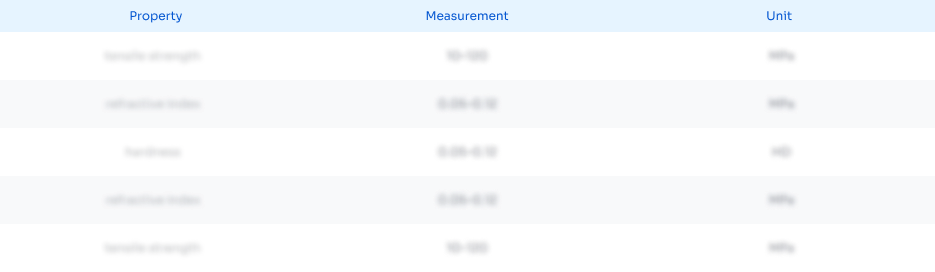
Abstract
Description
Claims
Application Information

- Generate Ideas
- Intellectual Property
- Life Sciences
- Materials
- Tech Scout
- Unparalleled Data Quality
- Higher Quality Content
- 60% Fewer Hallucinations
Browse by: Latest US Patents, China's latest patents, Technical Efficacy Thesaurus, Application Domain, Technology Topic, Popular Technical Reports.
© 2025 PatSnap. All rights reserved.Legal|Privacy policy|Modern Slavery Act Transparency Statement|Sitemap|About US| Contact US: help@patsnap.com