Heat treatment method for austenitic stainless steel pie forgings for nuclear power reactor internals
A technology of austenitic stainless steel and heat treatment method, applied in the field of heat treatment, can solve the problems of poor bottom performance of forgings, deterioration of forging performance uniformity, etc., achieve uniform performance, uniform structure, and ensure overall quality
- Summary
- Abstract
- Description
- Claims
- Application Information
AI Technical Summary
Problems solved by technology
Method used
Image
Examples
Embodiment Construction
[0019] Such as figure 1 As shown, the heat treatment method of the austenitic stainless steel pie-shaped forging for nuclear power reactor internal components of the present invention is used to heat treat a solid forging with a material of 0Cr19Ni10, a diameter of not less than 4000mm, and a thickness of not less than 400mm, comprising the following steps:
[0020] The first step is to place the forging in a heat treatment furnace and heat it to a temperature range of 400-450°C with the maximum power of the heat treatment furnace. The heat preservation time is 0.5-1 minute per 1 mm of forging thickness;
[0021] The purpose of this step is to control the temperature difference between the surface and the core of the forging to avoid cracking of the forging caused by blue embrittlement;
[0022] The second step is to continue to heat the workpiece, and heat the forging to a temperature range of 670-700 °C at a heating rate of no more than 50 °C / h. The holding time is 0.5-1 min...
PUM
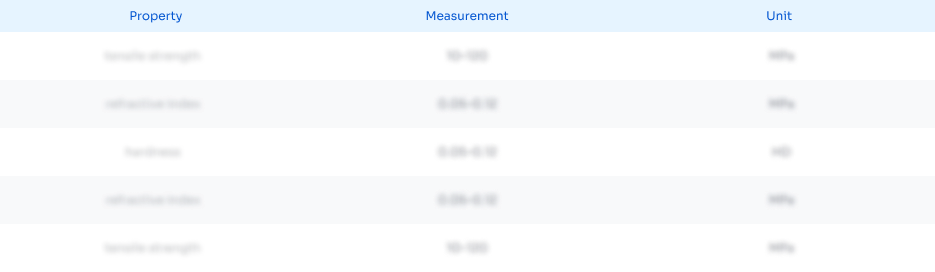
Abstract
Description
Claims
Application Information

- R&D
- Intellectual Property
- Life Sciences
- Materials
- Tech Scout
- Unparalleled Data Quality
- Higher Quality Content
- 60% Fewer Hallucinations
Browse by: Latest US Patents, China's latest patents, Technical Efficacy Thesaurus, Application Domain, Technology Topic, Popular Technical Reports.
© 2025 PatSnap. All rights reserved.Legal|Privacy policy|Modern Slavery Act Transparency Statement|Sitemap|About US| Contact US: help@patsnap.com