Synergic removal method for multiphase contaminant in sintering flue gas
A collaborative removal method, sintering flue gas technology, applied in separation methods, chemical instruments and methods, and separation of dispersed particles, etc., can solve problems such as difficulty in responding to load changes in time, containing dust and other impurities, and inability to process nitrogen oxides , to achieve the effect of improving the quality and economic benefits of by-products, increasing the purity and yield, and improving the aerosol phenomenon
- Summary
- Abstract
- Description
- Claims
- Application Information
AI Technical Summary
Problems solved by technology
Method used
Image
Examples
Embodiment Construction
[0028] Embodiments of the present invention will be further described below in conjunction with the accompanying drawings.
[0029] A method for synergistic removal of multi-phase pollutants from sintering flue gas. The method is as follows: pressurize the sintering flue gas after a dust removal, and partially oxidize it; the oxidized flue gas is catalytically oxidized to generate nitric acid and sulfuric acid, nitric acid and Sulfuric acid and ammonia water are neutralized to produce ammonium sulfate and ammonium nitrate, and the mixed solution of ammonium sulfate and ammonium nitrate is sent to the ammonium sulfate and ammonium nitrate evaporation crystallization system; the flue gas after catalytic oxidation is demisted and then chemically agglomerated and purified for secondary dust removal. and discharge.
[0030] see figure 1 and figure 2 , the specific steps are:
[0031] 1) Pass the sintering flue gas into the primary dust collector 1 for primary dust removal to re...
PUM
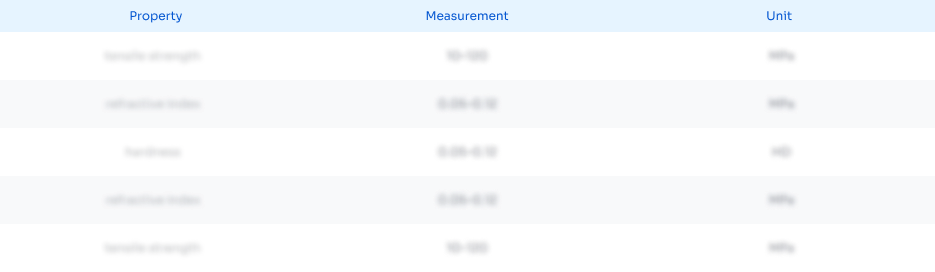
Abstract
Description
Claims
Application Information

- R&D Engineer
- R&D Manager
- IP Professional
- Industry Leading Data Capabilities
- Powerful AI technology
- Patent DNA Extraction
Browse by: Latest US Patents, China's latest patents, Technical Efficacy Thesaurus, Application Domain, Technology Topic, Popular Technical Reports.
© 2024 PatSnap. All rights reserved.Legal|Privacy policy|Modern Slavery Act Transparency Statement|Sitemap|About US| Contact US: help@patsnap.com