Capacitance detection system and capacitance detection method based on machine vision
A capacitance detection and machine vision technology, used in instruments, measuring devices, measuring electrical variables, etc., can solve problems such as lead bar scratches, blistering, casing length, etc.
- Summary
- Abstract
- Description
- Claims
- Application Information
AI Technical Summary
Problems solved by technology
Method used
Image
Examples
Embodiment 1
[0082] Such as figure 1 As shown, the capacitance detection system of Embodiment 1 includes a material inlet subsystem, a conveyor belt system, a closed optical chamber system, an electrical installation box system, a man-machine interface subsystem, and an automatic box packing subsystem. Among them, the material inlet subsystem includes the material bin, the vibrating material tray and the capacitor angle adjustment device; the conveyor belt system includes the device conveyor belt system, the device rotating table (smc production), and the material feeding and grabbing device; the optical room includes the optical image acquisition system, the optical room clean Cooling exhaust system, air purification FFU system; electrical installation box includes system power pool, algorithm main control subsystem, motion control subsystem. The device conveyor belt system includes five parts: the conveyor belt for the inlet part, the side defect detection conveyor belt, the bottom defec...
Embodiment 2
[0116] Different from Example 1, as Figure 22 As shown, it also includes an automatic boxing subsystem, which is based on (1) the number of layers of capacitors supported by a single box; (2) the number of rows of capacitors per layer; (3) the number of columns of capacitors per layer; (4) the number of capacitors diameter and height. And other parameters are automatically calculated to control the operating scale parameters of the motion system.
Embodiment 3
[0118] It is a capacitance detection method based on machine vision, including:
[0119] Capacitance sorting step, enter the lower system from the vertical direction of the vibrating tray;
[0120] Device size discrimination step, this step is to use an industrial camera to collect the size of the capacitor to be measured, including whether the height and diameter are consistent with the predetermined value, and automatically reject those that do not match; the specific implementation process is as follows: a. The photoelectric sensor placed on the capacitor conveyor belt , the capacitance is detected, and the photoelectric sensor returns the effective signal to the control system; b. The control system sends a corresponding control signal to control the light source and camera of the size discrimination subsystem for data collection; c. The image data is sent back to the image processing platform; d. The image processing platform judges whether the current capacitor size is q...
PUM
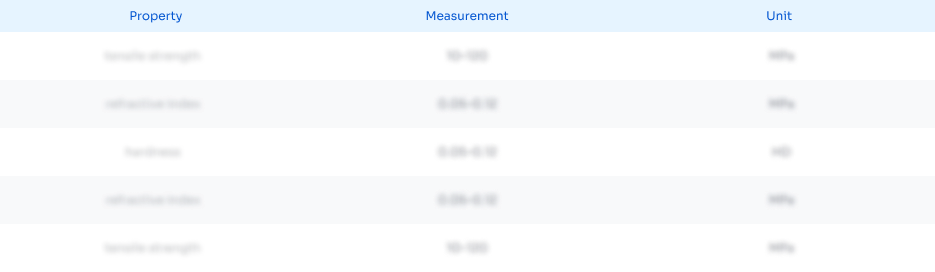
Abstract
Description
Claims
Application Information

- R&D
- Intellectual Property
- Life Sciences
- Materials
- Tech Scout
- Unparalleled Data Quality
- Higher Quality Content
- 60% Fewer Hallucinations
Browse by: Latest US Patents, China's latest patents, Technical Efficacy Thesaurus, Application Domain, Technology Topic, Popular Technical Reports.
© 2025 PatSnap. All rights reserved.Legal|Privacy policy|Modern Slavery Act Transparency Statement|Sitemap|About US| Contact US: help@patsnap.com