Cold molding glue water and preparation method thereof
A glue and cold-making technology, applied in the directions of starch-derived adhesives, adhesive types, etc., can solve the problems of high production cost, slow initial solidification speed, running corrugation, etc., to reduce production costs, fast initial solidification speed, Avoid the runaway effect
- Summary
- Abstract
- Description
- Claims
- Application Information
AI Technical Summary
Problems solved by technology
Method used
Examples
Embodiment 1
[0034] Prepare 400 parts of tap water, 90 parts of cornstarch, 1.5 parts of borax, 3.5 parts of concentrated sulfuric acid, 0.02 parts of tributyl phosphate, 0.12 parts of potassium permanganate, 1.5 parts of masking agent, and 8 parts of hydrogen Sodium oxide, 0.01 part of drier, and 0.1 part of sodium sulfite are for use; wherein, the concentration of the concentrated sulfuric acid is 85%, and the drier is an inorganic drier.
[0035] Afterwards, the cornstarch is oxidized
[0036] Put corn starch and 80% tap water together, stir well to make starch emulsion; while stirring, add concentrated sulfuric acid diluted to 30% and 3% potassium permanganate solution, stir well and place at room temperature 10 hours, carry out oxidation reaction, make starch emulsion become pure white starch emulsion;
[0037] Afterwards, rinse
[0038] Add the remaining tap water to the pure white starch emulsion, and stir for 8 minutes. After standing for an hour at room temperature, remove the u...
Embodiment 2
[0048] Prepare 500 parts of tap water, 100 parts of corn starch, 1.8 parts of borax, 4.0 parts of concentrated sulfuric acid, 0.04 parts of tributyl phosphate, 0.13 parts of potassium permanganate, 1.7 parts of masking agent, 9 parts of Sodium hydroxide, 0.02 part of drier, 0.13 part of sodium sulfite, set aside. Wherein, the concentration of the concentrated sulfuric acid is 85%, and the drier is an inorganic drier.
[0049] Afterwards, the cornstarch is oxidized
[0050] Put corn starch and 80% tap water together, stir well to make starch emulsion; while stirring, add concentrated sulfuric acid diluted to 30% and 3% potassium permanganate solution, stir well and place at room temperature 13 hours, carry out oxidation reaction, make starch emulsion become pure white starch emulsion;
[0051] Afterwards, rinse
[0052] Add the remaining tap water to the pure white starch emulsion, and stir for 9 minutes. After standing for an hour at room temperature, remove the upper layer...
Embodiment 3
[0062] Prepare 600 parts of tap water, 95 parts of corn starch, 2.0 parts of borax, 4.5 parts of concentrated sulfuric acid, 0.06 parts of tributyl phosphate, 0.15 parts of potassium permanganate, 2.0 parts of masking agent, 10 parts of Sodium hydroxide, 0.03 part of drier, 0.15 part of sodium sulfite, set aside. Wherein, the concentration of the concentrated sulfuric acid is 85%, and the drier is an inorganic drier.
[0063] Afterwards, the cornstarch is oxidized
[0064] Put cornstarch and 80% tap water together and stir well to make starch emulsion. While stirring, add diluted 30% concentrated sulfuric acid and 3% potassium permanganate solution, stir evenly and place it at room temperature for 15 hours to carry out oxidation reaction, so that the starch emulsion becomes pure white starch emulsion.
[0065] Afterwards, rinse
[0066] Add the remaining tap water to the pure white starch emulsion, and stir for 10 minutes. After standing at room temperature for one hour, re...
PUM
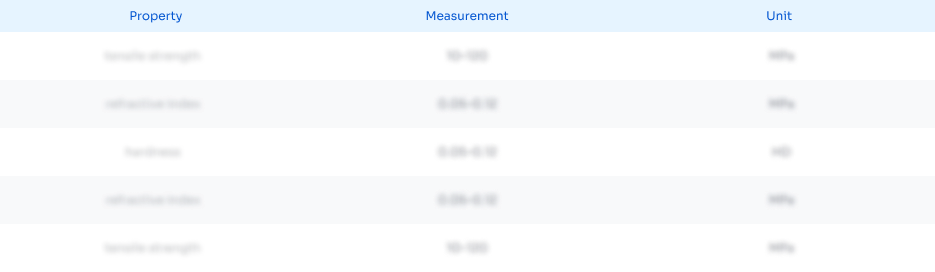
Abstract
Description
Claims
Application Information

- Generate Ideas
- Intellectual Property
- Life Sciences
- Materials
- Tech Scout
- Unparalleled Data Quality
- Higher Quality Content
- 60% Fewer Hallucinations
Browse by: Latest US Patents, China's latest patents, Technical Efficacy Thesaurus, Application Domain, Technology Topic, Popular Technical Reports.
© 2025 PatSnap. All rights reserved.Legal|Privacy policy|Modern Slavery Act Transparency Statement|Sitemap|About US| Contact US: help@patsnap.com