Nonlinear ultrasound evaluating method for impact fatigue damage of metal bonding interface
A non-linear ultrasonic and impact fatigue technology, which is applied in the direction of analyzing solids using sound waves/ultrasonic waves/infrasonic waves, can solve problems such as fatigue damage, insensitivity to degradation of mechanical properties of materials, and achieve the effect of ensuring safe operation
- Summary
- Abstract
- Description
- Claims
- Application Information
AI Technical Summary
Problems solved by technology
Method used
Image
Examples
Embodiment Construction
[0024] exist figure 1 , including: an oscilloscope 1, a host computer 2, a computer 3, a pre-attenuation and low-pass filter module 4, an ultrasonic excitation device 5, and an ultrasonic receiving device 7. The model of oscilloscope 1 is TDS3034B, the model of host 2 is Ritec SNAP-0.25-7-G2, and the model of pre-attenuation and low-pass filter module 4 is RLP-2. Utilize the coaxial cable to connect the signal output end A of the main frame 2 with the input end of the pre-attenuation and low-pass filter module 4, the output end of the pre-attenuation and low-pass filter module 4 is connected with the ultrasonic excitation device 5, and the ultrasonic receiving device 7 The signal is connected to the receiver B of the host computer 2, and the signal monitoring port C of the host computer 2 is connected to the oscilloscope 1. Both the ultrasonic excitation device 5 and the ultrasonic receiving device 7 are ultrasonic transducers.
[0025] A non-linear ultrasonic evaluation met...
PUM
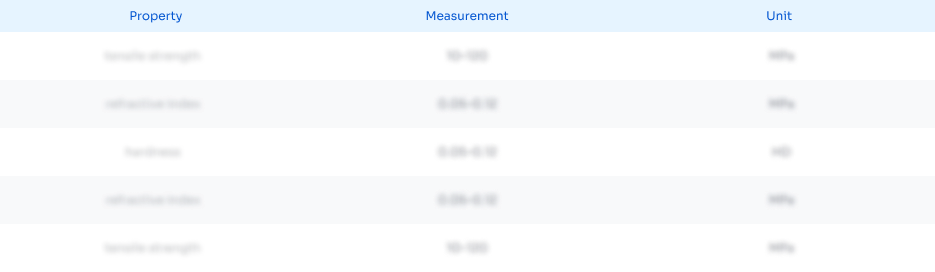
Abstract
Description
Claims
Application Information

- R&D
- Intellectual Property
- Life Sciences
- Materials
- Tech Scout
- Unparalleled Data Quality
- Higher Quality Content
- 60% Fewer Hallucinations
Browse by: Latest US Patents, China's latest patents, Technical Efficacy Thesaurus, Application Domain, Technology Topic, Popular Technical Reports.
© 2025 PatSnap. All rights reserved.Legal|Privacy policy|Modern Slavery Act Transparency Statement|Sitemap|About US| Contact US: help@patsnap.com