Double reheat power station boiler with three rear flues and double rear baffles and capable of recycling jet flow flue gas
A flue gas recirculation and secondary reheating technology, which is applied in lighting and heating equipment, steam superheating, steam generation, etc., can solve problems such as rising boiler exhaust temperature, increasing power consumption of induced draft fans, and large power consumption. To achieve the effect of saving investment
- Summary
- Abstract
- Description
- Claims
- Application Information
AI Technical Summary
Problems solved by technology
Method used
Image
Examples
Embodiment 1
[0034] Example 1: Three flue double baffles at the tail plus jet flue gas recirculation and secondary reheating power station boiler scheme
[0035] Combine now figure 1 Taking a 600MW grade secondary reheat Π-type power plant boiler with main steam temperature / reheat steam temperature 605°C / 623°C / 623°C as an example to illustrate the optimal way to realize the invention.
[0036]The power plant boiler with three flues and double baffles at the tail and jet flue gas recirculation and secondary reheating of the present invention includes a furnace and a burner (1), a panel superheater (2), a medium-temperature reheater (3), and a high-temperature superheater (4), primary high-temperature reheater (5), secondary high-temperature reheater (6), folding smoke angle (7), wind-smoke injector shut-off baffle (8), temperature-regulating air-smoke injector ( 9), injector deactivation protection cooling wind baffle (10), separated secondary air wind box (11), economizer (12), secondary ...
PUM
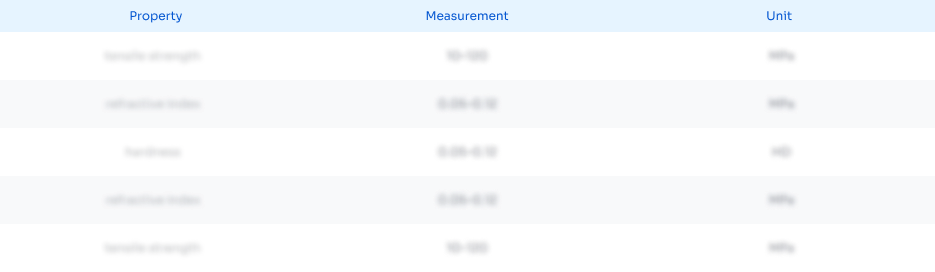
Abstract
Description
Claims
Application Information

- Generate Ideas
- Intellectual Property
- Life Sciences
- Materials
- Tech Scout
- Unparalleled Data Quality
- Higher Quality Content
- 60% Fewer Hallucinations
Browse by: Latest US Patents, China's latest patents, Technical Efficacy Thesaurus, Application Domain, Technology Topic, Popular Technical Reports.
© 2025 PatSnap. All rights reserved.Legal|Privacy policy|Modern Slavery Act Transparency Statement|Sitemap|About US| Contact US: help@patsnap.com