Anti-scratching coating of electromechanical equipment
A technology of electromechanical equipment and coating, applied in the direction of coating, etc., can solve problems such as surface erosion, abandoning coating, and inability to use for a long time, and achieve good wear-resistant and scratch-resistant performance, protection of electromechanical equipment, and long-lasting effects of electromechanical equipment
- Summary
- Abstract
- Description
- Claims
- Application Information
AI Technical Summary
Problems solved by technology
Method used
Examples
Embodiment 1
[0010] An anti-scratch coating for electromechanical equipment, wherein: the coating is composed of the following components in parts by mass: 45 parts of epoxy modified silicone resin, 12 parts of phenolic resin, 12 parts of barium sulfate, 5 parts of titanium dioxide, white carbon 5 parts black, 7 parts aminosiloxane, 5 parts aluminum silicate fiber and 10 parts phenyl glycidyl ether.
Embodiment 2
[0012] An anti-scratch coating for electromechanical equipment, wherein: the coating is composed of the following components in parts by mass: 65 parts of epoxy modified silicone resin, 22 parts of phenolic resin, 18 parts of barium sulfate, 12 parts of titanium dioxide, white carbon 9 parts black, 12 parts aminosiloxane, 10 parts aluminum silicate fiber and 25 parts phenyl glycidyl ether.
Embodiment 3
[0014] An anti-scratch coating for electromechanical equipment, wherein: the coating is composed of the following components in parts by mass: 60 parts of epoxy-modified silicone resin, 18 parts of phenolic resin, 16 parts of bentonite, 9 parts of titanium dioxide, white carbon black 7 parts, 8 parts of aminosiloxane, 8 parts of aluminum silicate fiber and 22 parts of butyl glycidyl ether.
PUM
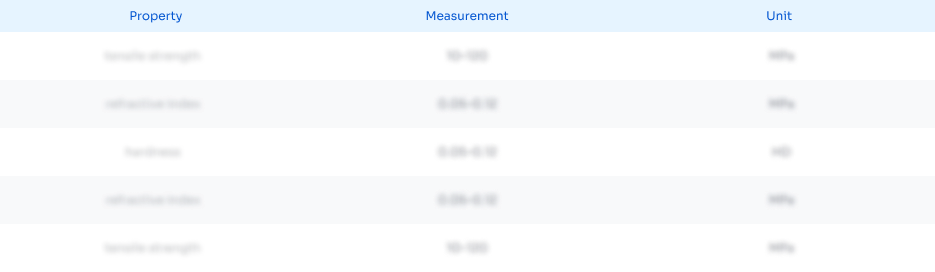
Abstract
Description
Claims
Application Information

- R&D Engineer
- R&D Manager
- IP Professional
- Industry Leading Data Capabilities
- Powerful AI technology
- Patent DNA Extraction
Browse by: Latest US Patents, China's latest patents, Technical Efficacy Thesaurus, Application Domain, Technology Topic, Popular Technical Reports.
© 2024 PatSnap. All rights reserved.Legal|Privacy policy|Modern Slavery Act Transparency Statement|Sitemap|About US| Contact US: help@patsnap.com