Method for preparing mixed dibasic acid mono-L-menthyl acetate by using nylon acid
A technology of mixing dibasic acid and nylon acid, applied in the preparation of carboxylate, chemical instruments and methods, preparation of organic compounds, etc., can solve problems such as reports on the research of synthetic methods, and achieve significant economic value and high yield , the effect of generating a simple process
- Summary
- Abstract
- Description
- Claims
- Application Information
AI Technical Summary
Problems solved by technology
Method used
Image
Examples
Embodiment 1
[0020] Add 75g of nylon acid and 120g of acetic anhydride to a 500ml three-neck flask equipped with a thermometer and a condenser tube and heat to reflux for 6 hours. Distilled under reduced pressure to remove acetic acid and remaining acetic anhydride, added 100 g of extraction solvent toluene, stirred, heated to reflux, cooled and filtered to obtain 11.0 g of crude adipic acid, which was recrystallized from water to obtain 9.0 g of adipic acid with a content of 98.5%. Evaporate part of the solvent from the filtrate under reduced pressure, add 0.9g of catalyst DMAP and 78g of menthol, heat at 100°C for 9 hours, filter, add 200g of 5% sodium carbonate solution by mass percentage, stir and separate layers, add 3N hydrochloric acid to the water layer, and adjust the pH value 3, stirred, extracted with chloroform, dried the organic layer, filtered and distilled off the solvent under pressure, and dried to obtain 132.4 g of mixed dibasic acid mono-L-menthyl ester, with a total cont...
Embodiment 2
[0022] Add 75g of nylon acid and 120g of acetic anhydride to a 500ml three-neck flask equipped with a thermometer and a condenser tube and heat to reflux for 6 hours. Distilled under reduced pressure to remove acetic acid and the remaining acetic anhydride, added 100 g of chloroform as an extraction solvent, stirred, heated to reflux, cooled and filtered to obtain 10.2 g of crude adipic acid, which was recrystallized from water to obtain 8.4 g of adipic acid with a content of 98.6%. Part of the solvent was evaporated from the filtrate under reduced pressure, 0.9 g of catalyst dipotassium hydrogen phosphate and 78 g of menthol were added, heated to reflux for 8 hours, filtered, 200 g of a 5% sodium carbonate solution by mass percentage was added, the layers were stirred, and 3N hydrochloric acid was added to the water layer to adjust The pH value was 1, stirred, extracted with chloroform, dried the organic layer, filtered and distilled off the solvent under pressure, and dried t...
Embodiment 3
[0024] Add 75g of nylon acid and 120g of acetic anhydride to a 500ml three-neck flask equipped with a thermometer and a condenser tube and heat to reflux for 6 hours. Distilled under reduced pressure to remove acetic acid and the remaining acetic anhydride, added 100 g of petroleum ether as an extraction solvent, stirred, heated to reflux, cooled and filtered to obtain 12.0 g of crude adipic acid, which was recrystallized from water to obtain 9.2 g of adipic acid with a content of 98.1%. Evaporate part of the solvent from the filtrate under reduced pressure, add 0.9 g of catalyst sodium sulfate and 78 g of menthol, heat at 120 ° C for 6 hours, filter, add 200 g of 5% by mass sodium carbonate solution, stir and separate layers, add 3N hydrochloric acid to the water layer, and adjust the pH The value was 2, stirred, extracted with chloroform, dried the organic layer, filtered and distilled off the solvent under pressure, and dried to obtain 134.3 g of mixed dibasic acid mono-L-me...
PUM
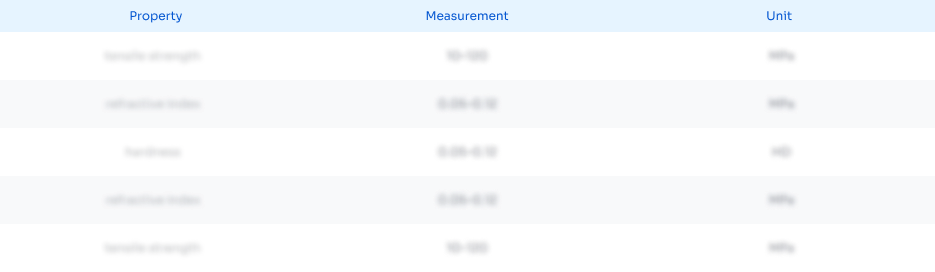
Abstract
Description
Claims
Application Information

- R&D Engineer
- R&D Manager
- IP Professional
- Industry Leading Data Capabilities
- Powerful AI technology
- Patent DNA Extraction
Browse by: Latest US Patents, China's latest patents, Technical Efficacy Thesaurus, Application Domain, Technology Topic, Popular Technical Reports.
© 2024 PatSnap. All rights reserved.Legal|Privacy policy|Modern Slavery Act Transparency Statement|Sitemap|About US| Contact US: help@patsnap.com