Multi-functional spindle mechanism used for small deep holes electrical discharge machining
A multi-functional, electric spark technology, applied in the direction of electric processing equipment, metal processing equipment, manufacturing tools, etc., can solve the problem that the operation process of electrode replacement is not simple enough, affects the accuracy of aperture and processing efficiency, and the error of electrode end rotation radial runout is large, etc. To solve the problem, achieve the effect of facilitating electrode creep feeding and replacement, improving chip removal ability, and reducing hardware cost
- Summary
- Abstract
- Description
- Claims
- Application Information
AI Technical Summary
Problems solved by technology
Method used
Image
Examples
Embodiment
[0085] 2. The specific operation steps and action process of gas film hole processing
[0086] Such as figure 1 As shown, taking the processing of a row of air film holes with an inclination angle of 40° to the blade surface and Φ0.5mm as an example, the specific operation steps and action process are explained.
[0087] (1) Electrode installation
[0088] Connect the main shaft with the Z axis, each of the wire storage tubes 38 has a Φ0.4mm electrode to be replaced, and the lower guide 42 seals the water tank 29; the first electromagnet 62 is energized, the second electromagnet 110 is energized, and the normally closed clip mechanism and sealing mechanism Open, the normally open clip mechanism is closed, push the handle 36 to make the electrode 10 fall freely to the position of the normally open clip mechanism, feed the electrode 10 to the set position, the first electromagnet 62 is powered on, and the second electromagnet 110 is powered off; push the handle 36 causes the l...
PUM
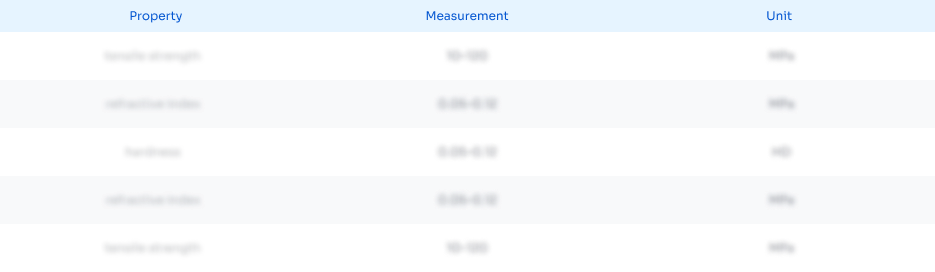
Abstract
Description
Claims
Application Information

- R&D
- Intellectual Property
- Life Sciences
- Materials
- Tech Scout
- Unparalleled Data Quality
- Higher Quality Content
- 60% Fewer Hallucinations
Browse by: Latest US Patents, China's latest patents, Technical Efficacy Thesaurus, Application Domain, Technology Topic, Popular Technical Reports.
© 2025 PatSnap. All rights reserved.Legal|Privacy policy|Modern Slavery Act Transparency Statement|Sitemap|About US| Contact US: help@patsnap.com