Low carbon alkane dehydrogenation catalyst and its preparation method and application
A dehydrogenation catalyst, a technology for low-carbon alkanes, applied in the fields of hydrocarbons, hydrocarbons, chemical instruments and methods, etc., can solve the problems of jeopardizing the catalytic performance of the formula, the incomplete reduction of chromium, and reducing the selectivity of olefins, etc. Fewer fractions, less cracking, high selectivity
- Summary
- Abstract
- Description
- Claims
- Application Information
AI Technical Summary
Problems solved by technology
Method used
Examples
Embodiment 1
[0023] Preparation of alumina carrier containing La: After mixing an appropriate amount of 0.98Mol / L aluminum trichloride solution and 0.01Mol / L lanthanum nitrate solution, add an appropriate amount of ammonia water with a mass fraction of 8%, and place it at 60-80°C Mix evenly in the neutralization tank, control the pH value to 7.0~9.0, filter, wash with water, and acidify, pressurize into balls in the oil ammonia column, dry, age, and roast at 650°C for 4 hours. Select the above-mentioned La-containing spherical alumina with a diameter of 1.0~2.0mm as the carrier to load the active component chromium, and select the precursor of chromium as chromic acid, immerse at room temperature for 5 hours, dry at 120°C for 5 hours, and bake at 600°C for 4 hours . The prepared catalyst is denoted as A, contains chromium oxide 15% by weight in the catalyst, and contains lanthanum oxide 1.2%.
Embodiment 2
[0029] Preparation of alumina carrier containing La: After mixing an appropriate amount of 0.98Mol / L aluminum trichloride solution and 0.01Mol / L lanthanum nitrate solution, add an appropriate amount of 8% ammonia water with a mass fraction of Mix evenly in the neutralization tank, control the pH value to 7.0~9.0, filter, wash with water, and acidify, pressurize into balls in the oil ammonia column, dry, age, and roast at 650°C for 4 hours. Select the La-containing spherical alumina with a diameter of 1.0-2.0mm as the carrier to load the active component chromium. The precursor of the selected chromium is chromium nitrate. After 5 hours of immersion at room temperature, it is dried at 120°C for 5 hours, and roasted at 600°C for 4 hours. Hour. The above-mentioned catalyst was loaded and immersed in copper nitrate solution, after immersing at room temperature for 5 hours, it was dried at 120°C for 5 hours, and then calcined at 600°C for 4 hours. The prepared catalyst is denoted ...
Embodiment 3
[0031]Preparation of alumina carrier containing La: After mixing an appropriate amount of 0.98Mol / L aluminum trichloride solution and 0.01Mol / L lanthanum nitrate solution, add an appropriate amount of 8% ammonia water with a mass fraction of Mix evenly in the neutralization tank, control the pH value to 7.0~9.0, filter, wash with water, and acidify, pressurize into balls in the oil ammonia column, dry, age, and roast at 650°C for 4 hours. Select the La-containing spherical alumina with a diameter of 1.0~2.0mm as the carrier to load the active component chromium. The precursor of the selected chromium is chromium acetate. After 5 hours of immersion at room temperature, it is dried at 120°C for 5 hours, and baked at 600°C for 4 hours. Hour. The catalyst was impregnated in a zinc nitrate solution for 5 hours at room temperature, then dried at 120°C for 5 hours, and calcined at 600°C for 4 hours. The prepared catalyst is denoted as D, containing chromium oxide 20% by weight in th...
PUM
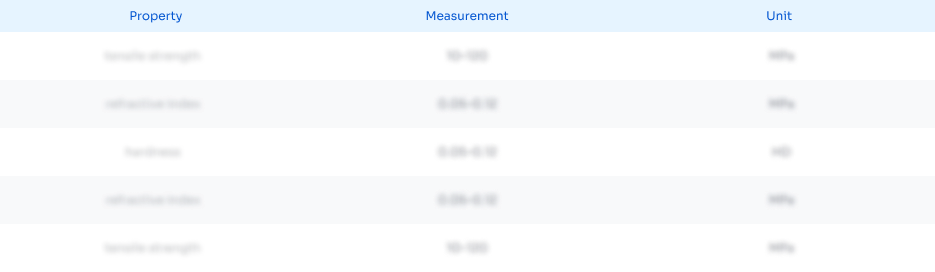
Abstract
Description
Claims
Application Information

- R&D
- Intellectual Property
- Life Sciences
- Materials
- Tech Scout
- Unparalleled Data Quality
- Higher Quality Content
- 60% Fewer Hallucinations
Browse by: Latest US Patents, China's latest patents, Technical Efficacy Thesaurus, Application Domain, Technology Topic, Popular Technical Reports.
© 2025 PatSnap. All rights reserved.Legal|Privacy policy|Modern Slavery Act Transparency Statement|Sitemap|About US| Contact US: help@patsnap.com