Method and device for controlling material drying temperature of cement production line with waste heat power generation
A technology of drying temperature and waste heat power generation, which is applied in cement production, drying, drying machines, etc., can solve the problems of reduced output, unstable cement quality, and increased energy consumption of cement clinker, so as to improve output and quality, The effect of maintaining stable operation and reducing the difficulty of operation
- Summary
- Abstract
- Description
- Claims
- Application Information
AI Technical Summary
Problems solved by technology
Method used
Image
Examples
Embodiment Construction
[0018] exist figure 1 In the process, the electric louver valve 2 is installed in the exhaust gas bypass pipeline at the kiln tail, the electric louver valve 3 is installed in the exhaust gas pipeline at the boiler inlet, and the temperature sensor 6 is installed at the inlet pipeline of the drying system at the kiln tail, and the temperature signal and the opening degree of the electric valve are input and output The signal is connected to the computer control system.
[0019] exist figure 2 In the process, an electric shutter valve 2 is installed in the waste gas bypass pipe of the kiln head, an electric shutter valve 3 is installed in the exhaust gas pipe at the boiler inlet, a temperature sensor 5 is installed at the inlet pipe of the kiln head material drying system, and the temperature signal and the opening degree of the electric valve are input, The output signal is connected to the computer control system.
[0020] image 3 Shown is the implementation of the contr...
PUM
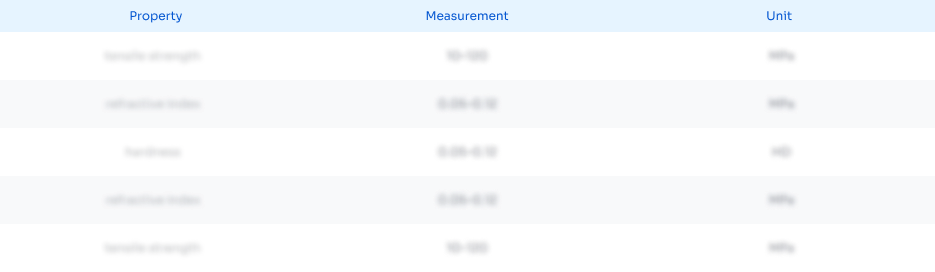
Abstract
Description
Claims
Application Information

- Generate Ideas
- Intellectual Property
- Life Sciences
- Materials
- Tech Scout
- Unparalleled Data Quality
- Higher Quality Content
- 60% Fewer Hallucinations
Browse by: Latest US Patents, China's latest patents, Technical Efficacy Thesaurus, Application Domain, Technology Topic, Popular Technical Reports.
© 2025 PatSnap. All rights reserved.Legal|Privacy policy|Modern Slavery Act Transparency Statement|Sitemap|About US| Contact US: help@patsnap.com