Treatment process of processing wastewater after nuclear power equipment forging-casting part welding
A treatment process and casting and forging technology, which is applied in the field of processing waste water after welding of nuclear power equipment castings and forgings. It can solve the problems that it is difficult to achieve the ideal treatment effect, and achieve the effects of easy maintenance and management, good treatment effect and simple equipment operation.
- Summary
- Abstract
- Description
- Claims
- Application Information
AI Technical Summary
Problems solved by technology
Method used
Image
Examples
Embodiment Construction
[0027] A process for treating waste water after welding of castings and forgings of nuclear power equipment, comprising the following steps:
[0028] (1) After the welding of nuclear power equipment castings and forgings, the processing wastewater is divided into intermittently discharged high-concentration wastewater and continuous discharge of low-concentration wastewater; high-concentration wastewater first enters the 1# grid well 1, and then removes large impurities through artificial grid sieves Through the 1# gate well 2, it enters the high-concentration wastewater pool 3 for centralized collection, and finally enters the oil separation adjustment tank 4; the low-concentration wastewater first enters the 2# grid well 5, and after removing large impurities through the artificial grid screen, it passes through the 2# gate well 6 , and finally mixed with the quantitatively entered high-concentration wastewater in the oil separation adjustment tank 4. The oil separation adjus...
PUM
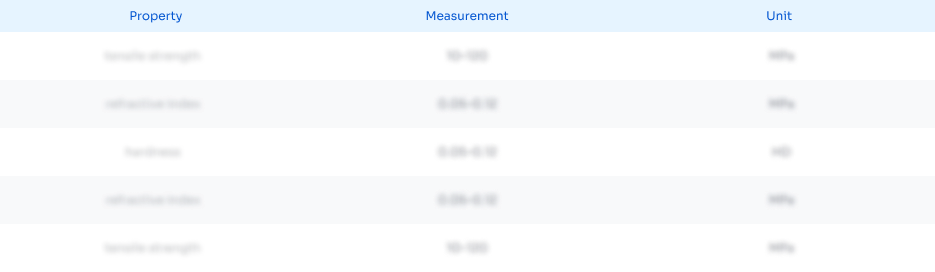
Abstract
Description
Claims
Application Information

- Generate Ideas
- Intellectual Property
- Life Sciences
- Materials
- Tech Scout
- Unparalleled Data Quality
- Higher Quality Content
- 60% Fewer Hallucinations
Browse by: Latest US Patents, China's latest patents, Technical Efficacy Thesaurus, Application Domain, Technology Topic, Popular Technical Reports.
© 2025 PatSnap. All rights reserved.Legal|Privacy policy|Modern Slavery Act Transparency Statement|Sitemap|About US| Contact US: help@patsnap.com