Copper rod manufacturing method and milling machine suitable for copper rod manufacturing method and capable of scoring
A manufacturing method and technology of copper rods, applied to milling machine equipment, manufacturing tools, details of milling machine equipment, etc., can solve the problems of high proportion of surface defects and large differences in ductility in the circumferential direction, etc., and achieve the effect of less proportion of defects
- Summary
- Abstract
- Description
- Claims
- Application Information
AI Technical Summary
Problems solved by technology
Method used
Image
Examples
Embodiment 1
[0027] Example 1, see figure 1 , A scoring milling machine, including a milling machine 1 and a scoring mechanism 3. The milling machine 1 is an existing milling machine.
[0028] The scoring mechanism 3 is located on the feed side of the milling machine 1. The scoring mechanism 3 includes a base plate 31, a blade driving mechanism 32 and a blade 33. The base plate 31 is provided with a sliding groove 311. The blade driving mechanism 32 includes a pair of blade fixing frames 321 and a fixing frame driving cylinder 322. A pair of blade holders 321 are located on both radial sides of the copper rod blank 5. The blade holder 321 includes a sliding rod 3212 extending in the up and down direction and a knife seat 3213 slidably connected to the sliding rod. The blade 33 is connected to the knife holder 3213 by a double-headed screw 3214. The blade edges 331 located on both radial sides of the copper rod blank 5 face the copper rod blank 5. The cylinder body of the fixed frame dri...
Embodiment 2
[0037] Example two, see image 3 The difference from the first embodiment is that it also includes a mounting seat 2, a floating raft 8 and a base 6 distributed in order from top to bottom. Both the milling machine 1 and the scoring mechanism 3 are fixed on the mounting base 2. The mounting base 2 is connected to the floating raft 8 through a number of vibration isolators 4. The floating raft 8 is connected to the base 6 through a number of vibration isolators 4. Specifically, there are 8 vibration isolators 4 (only 4 can be seen in the figure). Four of the eight vibration isolators 4 are used to support the mounting base 2 on the floating raft 8, and the other four vibration isolators are used to support the floating raft 8 on the base 6. The vibration isolator connecting the mounting base 2 and the floating raft 8 is staggered from the vibration isolator connecting the floating raft 8 and the base 6. The broadband vibration transmission between the mounting base 2 and the ...
Embodiment 3
[0052] The third embodiment, the difference from the second embodiment is: see Figure 8 End caps 829 are provided at both ends of the upper deformation channel 825 and the lower deformation channel 827. The upper inclined support plate of the upper inclined support plate 824 located between adjacent upper deformation channels 825, the lower inclined support plate of the lower inclined support plate 826 located between adjacent lower deformation channels 827, and the middle base plate 822 are located adjacent to each other. A damping channel 820 is provided on the part between the upper deformation channel and the lower deformation channel. Both the upper deformation channel 825 and the lower deformation channel 827 are filled with liquid (the liquid is not shown in the figure). The upper deformation channel 825 and the lower deformation channel 827 are provided with energy absorbing rods 83 suspended in the liquid. The extension direction of the energy absorbing rod 83 is the...
PUM
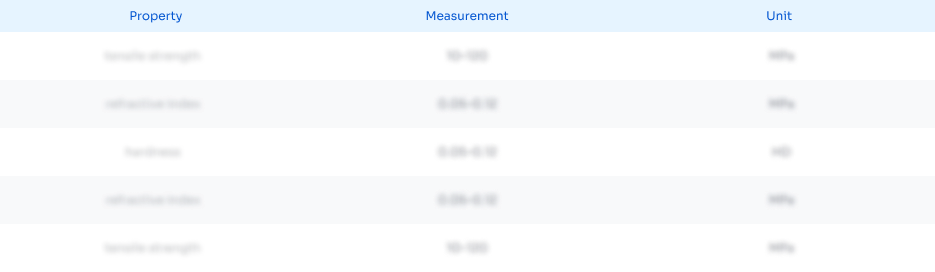
Abstract
Description
Claims
Application Information

- R&D Engineer
- R&D Manager
- IP Professional
- Industry Leading Data Capabilities
- Powerful AI technology
- Patent DNA Extraction
Browse by: Latest US Patents, China's latest patents, Technical Efficacy Thesaurus, Application Domain, Technology Topic, Popular Technical Reports.
© 2024 PatSnap. All rights reserved.Legal|Privacy policy|Modern Slavery Act Transparency Statement|Sitemap|About US| Contact US: help@patsnap.com