Porous ferric oxide/carbon nanometer plate composite material as well as preparation method thereof and application in preparing lithium ion battery
A technology for ferric oxide and lithium ion batteries, applied in the field of lithium ion batteries, can solve the problems of low theoretical capacity, poor cycle stability, low electronic conductivity, etc., achieve high volume specific capacity and volume energy density, and low preparation cost , the effect of high specific capacity
- Summary
- Abstract
- Description
- Claims
- Application Information
AI Technical Summary
Problems solved by technology
Method used
Image
Examples
Embodiment 1
[0042] After manually grinding ferrocene and ammonium sulfate with a mass ratio of 1:1, the mixture was put into a reaction kettle in an argon-filled glove box, and the reaction kettle was heated to 550 °C for 3 h. The black product in the reaction kettle was taken out and transferred to a tube furnace to be heated to 350 °C and kept for 1 h to obtain porous Fe2O3 / carbon nanosheet composites.
[0043] Preparation of the negative electrode: Using N-methyl-pyrrolidone (NMP) as the solvent, mix the above-mentioned nanosheets with the conductive agent acetylene black and the binder polyvinylidene fluoride (PVDF) according to the mass ratio of 8:1:1. Coated on the current collector, then dried at 120°C, rolled and formed after drying, and cut into pieces to obtain negative electrodes of required size.
[0044] Preparation of lithium-ion batteries: Add lithium iron phosphate, conductive agent acetylene black, and polyvinylidene fluoride (PVDF) with a weight ratio of 8:1:1 to N-methy...
Embodiment 2
[0048] After mechanically grinding ferrocene and ammonium sulfate with a mass ratio of 1:1.5, the mixture was put into a reaction kettle in a glove box filled with nitrogen, and the reaction kettle was heated to 550° C. for 3 hours. The black product in the reaction kettle was taken out and transferred to a tube furnace to be heated to 350 °C and kept for 1 h to obtain porous Fe2O3 / carbon nanosheet composites. Using the material obtained in this example as the negative electrode material, the same method as in Example 1 was used to prepare the lithium ion battery negative electrode and the lithium ion battery.
Embodiment 3
[0050] After mechanically stirring ferrocene and ammonium sulfate with a mass ratio of 1:0.5, the mixture was put into a reaction kettle in an argon-filled glove box, and the reaction kettle was heated to 550° C. for 1 hour. The black product in the reaction kettle was taken out and transferred to a tube furnace to be heated to 300 °C and kept for 0.5 h to obtain a porous ferric oxide / carbon nanosheet composite. Using the composite material obtained in this example as the negative electrode material, the same method as in Example 1 was used to prepare the lithium ion battery negative electrode and the lithium ion battery.
PUM
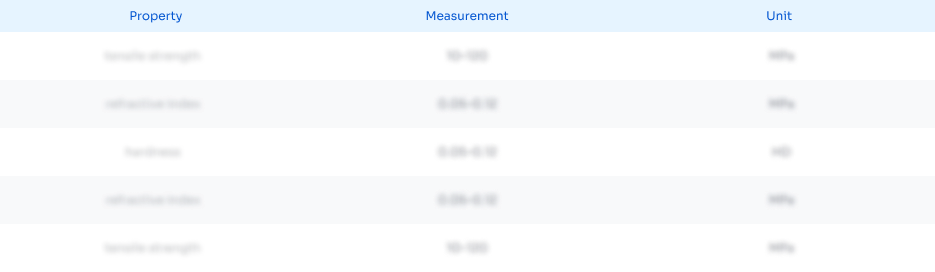
Abstract
Description
Claims
Application Information

- R&D
- Intellectual Property
- Life Sciences
- Materials
- Tech Scout
- Unparalleled Data Quality
- Higher Quality Content
- 60% Fewer Hallucinations
Browse by: Latest US Patents, China's latest patents, Technical Efficacy Thesaurus, Application Domain, Technology Topic, Popular Technical Reports.
© 2025 PatSnap. All rights reserved.Legal|Privacy policy|Modern Slavery Act Transparency Statement|Sitemap|About US| Contact US: help@patsnap.com