Spiral pipe robot
A pipeline robot, spiral technology, applied in the direction of special pipes, pipe components, mechanical equipment, etc., can solve the problems of drive wheel stuck, affect the reliability of pipeline robot operation, and cannot ensure the smooth operation of the robot, so as to ensure the convenience Effect
- Summary
- Abstract
- Description
- Claims
- Application Information
AI Technical Summary
Problems solved by technology
Method used
Image
Examples
Embodiment Construction
[0038] The specific implementation manner of the present invention will be described below in conjunction with the accompanying drawings.
[0039] See figure 1 , the present invention includes symmetrically arranged travel assemblies 1, a control assembly 2 is arranged between two sets of travel assemblies 1, and the travel assembly 1 and control assembly 2 are connected by telescopic joints 5 and universal joints 3.
[0040] See figure 1 , figure 2 , the structure of the walking assembly 1 is as follows: including the mounting frame 101, the mounting frame 101 is provided with a motor one 102, the output shaft of the motor one 102 is connected with the rotating frame 103 through a coupling, and the mounting frame 101 and the rotating frame 103 are evenly arranged along the circumference There are a plurality of roller mechanisms 104, and the roller mechanisms 104 of the mounting frame 101 and the roller mechanisms 104 of the rotating frame 103 are arranged in a staggered m...
PUM
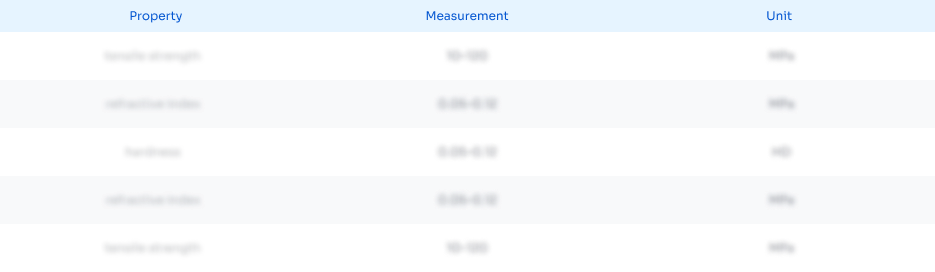
Abstract
Description
Claims
Application Information

- R&D
- Intellectual Property
- Life Sciences
- Materials
- Tech Scout
- Unparalleled Data Quality
- Higher Quality Content
- 60% Fewer Hallucinations
Browse by: Latest US Patents, China's latest patents, Technical Efficacy Thesaurus, Application Domain, Technology Topic, Popular Technical Reports.
© 2025 PatSnap. All rights reserved.Legal|Privacy policy|Modern Slavery Act Transparency Statement|Sitemap|About US| Contact US: help@patsnap.com