Modifier for regenerating and processing hybrid waste plastic injection part materials and usage method
A technology for processing modifiers and waste plastics, which is applied in the field of waste plastic recycling processing aids, can solve the problems of no substantial improvement in processing methods, poor compatibility, complex components, etc., and achieve increased use value, increased strength, improved compatibility effect
- Summary
- Abstract
- Description
- Claims
- Application Information
AI Technical Summary
Problems solved by technology
Method used
Examples
Embodiment 1
[0013] The mixed waste plastic injection molded part material recycling processing modifier of the present invention, its raw material formula is represented by weight ratio and includes the following components: maleic anhydride 1; chlorinated polyethylene 2; ethylene·vinyl acetate copolymer 3; benzene Ethylene·butadiene·styrene block copolymer 4; styrene 5, for later use; put the above-mentioned modifier raw material components into a high-speed mixer at a temperature of 110°C and mix evenly, then discharge and cool for later use.
[0014] The using method of modifying agent of the present invention operates according to the following steps:
[0015] (1) Classify the waste mixed plastic injection molded parts to obtain PE, PP and PS, as well as PA, PET, PVC and other mixed waste plastic injection molded parts wool;
[0016] (2) Crush, wash, dehydrate, dry and dehumidify all kinds of mixed waste plastic injection molding materials obtained from the above classification to obt...
Embodiment 2
[0020] This embodiment is basically the same as Embodiment 1, the difference is that:
[0021] The components and parts by weight of the mixed waste plastic injection molded part material recycling processing modifier according to the present invention are: maleic anhydride 2; chlorinated polyethylene 2.5; ethylene-vinyl acetate copolymer 4; styrene-butane ene-styrene block copolymer 5; styrene 6; put the above-mentioned modifier raw material components into a high-speed mixer at a temperature of 120°C and mix them.
[0022] The method of using the modifier of the present invention: (3) The amount of the modified modifier is 4% of the total weight after mixing, and the temperature is raised to 108°C at room temperature; (4) Use a plastic granulator Granulation was carried out under the temperature condition of 215° C., and the granulation time was 16 minutes.
Embodiment 3
[0024] This embodiment is basically the same as Embodiment 1, the difference is that:
[0025] The components and parts by weight of the mixed waste plastic injection molded part material recycling processing modifier according to the present invention are: maleic anhydride 4; chlorinated polyethylene 4.5; ethylene-vinyl acetate copolymer 6; styrene-butane ethylene-styrene block copolymer 7; styrene 7.5; put the above-mentioned modifier raw material components together into a high-speed mixer at a temperature of 118°C for mixing.
[0026] The method of using the modifier of the present invention: (3) The dosage of the modified modifier is 6% of the total weight after mixing, and the temperature is raised to 107°C at room temperature; (4) Use a plastic granulator Granulate under the temperature condition of 170 DEG C, and the granulation time is 20 minutes.
PUM
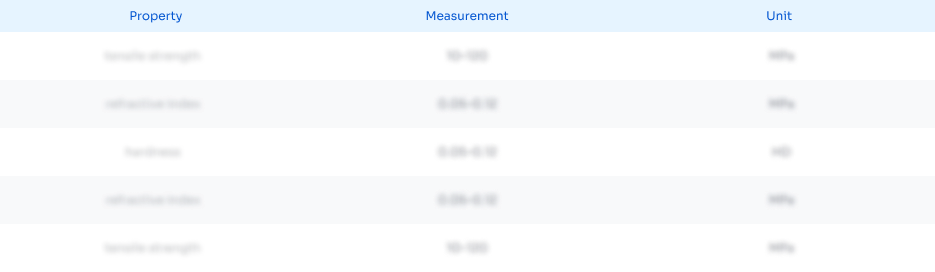
Abstract
Description
Claims
Application Information

- R&D
- Intellectual Property
- Life Sciences
- Materials
- Tech Scout
- Unparalleled Data Quality
- Higher Quality Content
- 60% Fewer Hallucinations
Browse by: Latest US Patents, China's latest patents, Technical Efficacy Thesaurus, Application Domain, Technology Topic, Popular Technical Reports.
© 2025 PatSnap. All rights reserved.Legal|Privacy policy|Modern Slavery Act Transparency Statement|Sitemap|About US| Contact US: help@patsnap.com