A processing technology of finless heat exchanger
A heat exchanger and processing technology, which is applied in heat exchange equipment, metal processing, metal processing equipment, etc., can solve the problems of low welding strength, easy stress at joints, deformation of flat tubes, etc., so as to improve the wetting performance. , Improve the effect of firmness and firm weld
- Summary
- Abstract
- Description
- Claims
- Application Information
AI Technical Summary
Problems solved by technology
Method used
Image
Examples
no. 1 approach
[0027] The processing technology of the finless heat exchanger includes the following steps:
[0028] (1) Machining sockets for flat tube insertion on the circumference of tube body 1, the distance between adjacent sockets is 2mm;
[0029] (2) Insert both ends of the flat tube 2 into the corresponding holes on the tube bodies at both ends;
[0030] (3) Set welding positioning tooling between the flat tubes; and make the flat tubes clamped in the card slot 7. In a group of flat tubes composed of multiple flat tubes, different numbers of welding are set according to the length of the flat tubes Positioning tooling;
[0031] (4) Apply solder paste on the tube body 1 and the flat tube 2 at the junction of the tube body and the flat tube;
[0032] (5) On both sides of the flat tube 2 are provided with strengthening electrodes attached to the circumferential wall of the tube body; the strengthening electrodes are U-shaped, and one side of the strengthening electrodes is an arc surface matchi...
no. 2 approach
[0036] The processing technology of the finless heat exchanger includes the following steps:
[0037] (1) Machining the hole for inserting the flat tube on the circumference of the tube body 1, the distance between adjacent holes is 3mm;
[0038] (2) Insert both ends of the flat tube 2 into the corresponding holes on the tube bodies at both ends;
[0039] (3) Set welding positioning tooling between the flat tubes; and make the flat tubes clamped in the card slot 7. In a group of flat tubes composed of multiple flat tubes, different numbers of welding are set according to the length of the flat tubes Positioning tooling;
[0040] (4) Apply solder paste on the tube body 1 and the flat tube 2 at the junction of the tube body and the flat tube;
[0041] (5) On both sides of the flat tube 2 are provided with strengthening electrodes attached to the circumferential wall of the tube body; the strengthening electrodes are U-shaped, and one side of the strengthening electrodes is an arc surface...
PUM
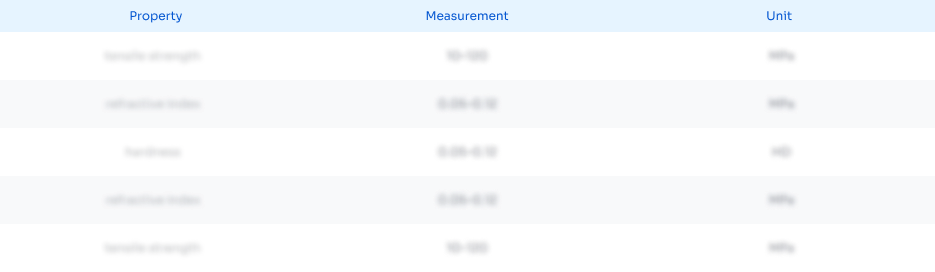
Abstract
Description
Claims
Application Information

- Generate Ideas
- Intellectual Property
- Life Sciences
- Materials
- Tech Scout
- Unparalleled Data Quality
- Higher Quality Content
- 60% Fewer Hallucinations
Browse by: Latest US Patents, China's latest patents, Technical Efficacy Thesaurus, Application Domain, Technology Topic, Popular Technical Reports.
© 2025 PatSnap. All rights reserved.Legal|Privacy policy|Modern Slavery Act Transparency Statement|Sitemap|About US| Contact US: help@patsnap.com