Composite material base for satellite antenna bearing cylinder and preparation method
A composite material, satellite antenna technology, applied in the direction of antenna support/installation device, etc., can solve the problems of low working reliability, low axial stiffness, poor thermal stability, etc. Good thermal stability
- Summary
- Abstract
- Description
- Claims
- Application Information
AI Technical Summary
Problems solved by technology
Method used
Image
Examples
Embodiment 1
[0043] Such as figure 1 , figure 2 , image 3As shown in Fig. 4, the composite material base used for the satellite antenna bearing cylinder of the present embodiment includes a lower base and an upper base installed above the lower base; the lower base includes an upper end cover 1 and a lower end cover 4, the The upper end cap 1 includes a circular upper end cap body 1-1 and a first cone 1-2 with a small upper part and a larger lower part arranged below the upper end cap body 1-1. The lower end cap includes a lower end cap body 4-1 and a set The second cone 4-2 with a large top and a small bottom above the lower end cover body, the upper end cover body 1-1 and the first cone 1-2 are integrated structures, the lower end cover body 4-1 and the second cone The two cones 4-2 have an integrated structure, and a first cylinder 2 is arranged between the upper end cover 1 and the lower end cover 4, and the upper inner wall of the first cylinder 2 is connected to the outer wall of...
Embodiment 2
[0064] This embodiment is the same as Embodiment 1, and the difference is that the angle between the cone surface of the first cone 1-2 and the vertical direction and the angle between the cone surface of the second cone 4-2 and the vertical direction The included angle is 10 degrees.
[0065] The base of this embodiment has the advantages of high axial stiffness, good thermal stability in high and low temperature environments, less negative mass, high modularity, good reliability, and excellent comprehensive performance. The axial modulus is ≥ 100GPa, and the glass transition The temperature is 210℃~220℃, and the quality is 40% lighter than that of aluminum alloy products.
Embodiment 3
[0067] This embodiment is the same as Embodiment 1, and the difference is that the angle between the cone surface of the first cone 1-2 and the vertical direction and the angle between the cone surface of the second cone 4-2 and the vertical direction The included angle is 1 degree.
[0068] The base of this embodiment has the advantages of high axial stiffness, good thermal stability in high and low temperature environments, less negative mass, high modularity, good reliability, and excellent comprehensive performance. The axial modulus is ≥ 100GPa, and the glass transition The temperature is 210℃~220℃, and the quality is 40% lighter than that of aluminum alloy products.
PUM
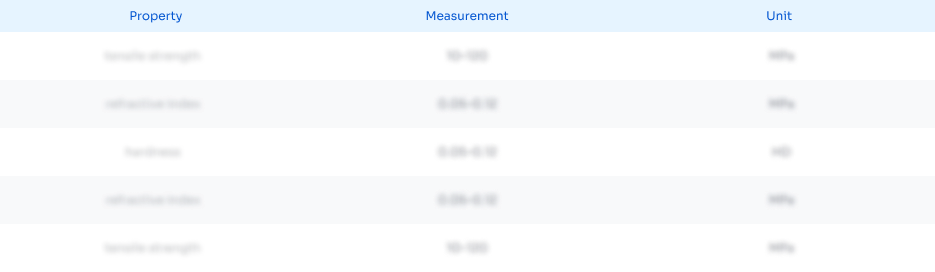
Abstract
Description
Claims
Application Information

- R&D
- Intellectual Property
- Life Sciences
- Materials
- Tech Scout
- Unparalleled Data Quality
- Higher Quality Content
- 60% Fewer Hallucinations
Browse by: Latest US Patents, China's latest patents, Technical Efficacy Thesaurus, Application Domain, Technology Topic, Popular Technical Reports.
© 2025 PatSnap. All rights reserved.Legal|Privacy policy|Modern Slavery Act Transparency Statement|Sitemap|About US| Contact US: help@patsnap.com