Heat-insulation and sound-insulation composite plate
A technology of thermal insulation and sound insulation and composite board, which is applied in thermal insulation, sound insulation, building components and other directions, can solve problems such as affecting the normal life of residents, poor working environment of workers, no sound insulation measures, etc., and achieves good sound insulation effect, good thermal insulation effect, and thermal insulation. good effect
- Summary
- Abstract
- Description
- Claims
- Application Information
AI Technical Summary
Problems solved by technology
Method used
Examples
Embodiment 1
[0014] The insulation board is polyethylene foam board, and the sound insulation board is rock wool board. Mix 120 parts of cement, 30 parts of expanded perlite, and 10 parts of silica evenly, then add 100 parts of hot water at 60-65°C and stir to make a sound insulation sticky board. Mixture, two layers of rock wool sound insulation boards are bonded with sound insulation adhesive between the two layers of insulation boards, and a layer of wooden moisture-proof board is glued on the outside of the two layers of insulation boards to make a thermal insulation and sound insulation composite board.
Embodiment 2
[0016] The insulation board is polyurethane foam board, and the sound insulation board is rock wool board. Mix 120 parts of cement, 30 parts of expanded perlite, and 10 parts of silica evenly, then add 100 parts of hot water at 60-65°C and stir to form a sound-proof bond. Two layers of rock wool sound insulation boards are bonded with sound insulation adhesive between the two layers of insulation boards, and a layer of wooden moisture-proof boards are glued on the outside of the two layers of insulation boards to make a thermal insulation and sound insulation composite board.
Embodiment 3
[0018] The insulation board is polystyrene foam board, and the sound insulation board is rock wool board. Mix 120 parts of cement, 30 parts of expanded perlite, and 10 parts of silica evenly, then add 100 parts of hot water at 60-65 °C and stir to make a sound insulation board. Adhesive, two layers of rock wool sound insulation boards are bonded with sound insulation adhesive between the two layers of insulation boards, and a layer of wooden moisture-proof board is glued on the outside of the two layers of insulation boards to make a thermal insulation and sound insulation composite board.
PUM
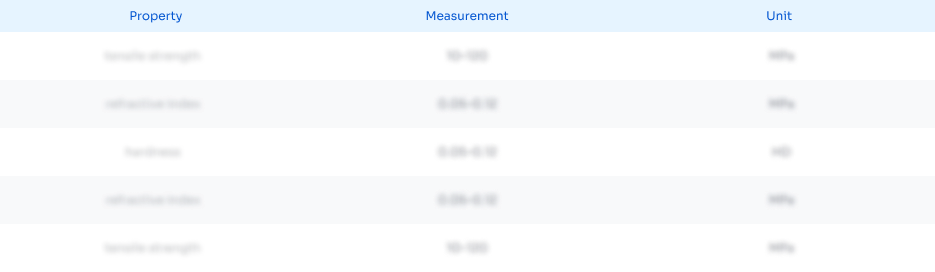
Abstract
Description
Claims
Application Information

- R&D
- Intellectual Property
- Life Sciences
- Materials
- Tech Scout
- Unparalleled Data Quality
- Higher Quality Content
- 60% Fewer Hallucinations
Browse by: Latest US Patents, China's latest patents, Technical Efficacy Thesaurus, Application Domain, Technology Topic, Popular Technical Reports.
© 2025 PatSnap. All rights reserved.Legal|Privacy policy|Modern Slavery Act Transparency Statement|Sitemap|About US| Contact US: help@patsnap.com