Printing and dyeing process of denim
A printing and dyeing process, denim technology, applied in dyeing, textile and paper making, dry cleaning fiber products, etc., can solve the problems of high cost, difficult quality, serious environmental pollution, etc.
- Summary
- Abstract
- Description
- Claims
- Application Information
AI Technical Summary
Problems solved by technology
Method used
Examples
Embodiment 1
[0016] A printing and dyeing process for denim, comprising the steps of:
[0017] 1) Treat the gray cloth with alkali, refining agent and hydrogen peroxide, and dehydrate and shape it;
[0018] 2) Slurry printing: To prepare printing paste, take 18 parts by mass of soda ash, 13 parts by mass of glycerin, 8 parts by mass of warm water, 80 parts by mass of etherified starch paste, 8 parts by mass of sodium bisulfite dihydrate formaldehyde, and 2 parts by mass of sulfur dye Prepare sulfur dye printing paste; get 45 parts by mass of etherified starch paste, 14 parts by mass of soda ash, 9 parts by mass of white powder, 8 parts by mass of glycerin, 8 parts by mass of anthraquinone vat dyes, and 25 parts by mass of warm water to prepare vat dye printing paste; Sulfur dye printing paste is used in conjunction with vat dye printing paste; the viscosity is controlled at 20000Pa·S, after uniform preparation, it is filtered with a 50-mesh screen, printed on a flat screen printing machine...
Embodiment 2
[0025] A printing and dyeing process for denim, comprising the steps of:
[0026] 1) Treat the gray cloth with alkali, refining agent and hydrogen peroxide, and dehydrate and shape it;
[0027] 2) Paste printing: To prepare printing paste, take 16 parts by mass of soda ash, 11 parts by mass of glycerin, 6 parts by mass of warm water, 75 parts by mass of etherified starch paste, 5 parts by mass of sodium bisulfite dihydrate formaldehyde, and 1 part by mass of sulfur dye Prepare sulfur dye printing paste; take 40 parts by mass of etherified starch paste, 12 parts by mass of soda ash, 7 parts by mass of white powder, 7 parts by mass of glycerin, 6 parts by mass of anthraquinone vat dyes, and 23 parts by mass of warm water to prepare vat dye printing paste; Sulfur dye printing paste is used in conjunction with vat dye printing paste; the viscosity is controlled at 15000Pa·S, after uniform preparation, it is filtered with a 40-mesh screen, printed on a flat screen printing machine,...
Embodiment 3
[0034] A printing and dyeing process for denim, comprising the steps of:
[0035] 1) Treat the gray cloth with alkali, refining agent and hydrogen peroxide, and dehydrate and shape it;
[0036] 2) Slurry printing: To prepare printing paste, take 17 parts by mass of soda ash, 12 parts by mass of glycerin, 6.8 parts by mass of warm water, 78 parts by mass of etherified starch paste, 5.8 parts by mass of sodium sulfoxylate dihydrate formaldehyde, and 1.2 parts by mass of sulfur dye Preparation of sulfur dye printing paste; take 43 parts by mass of etherified starch paste, 13 parts by mass of soda ash, 7.9 parts by mass of white powder, 7.8 parts by mass of glycerin, 6.8 parts by mass of anthraquinone vat dyes, and 24 parts by mass of warm water to prepare vat dye printing paste; Sulfur dye printing paste is used in conjunction with vat dye printing paste; the viscosity is controlled at 17000Pa·S, after uniform preparation, it is filtered with a 45-mesh screen, printed on a flat s...
PUM
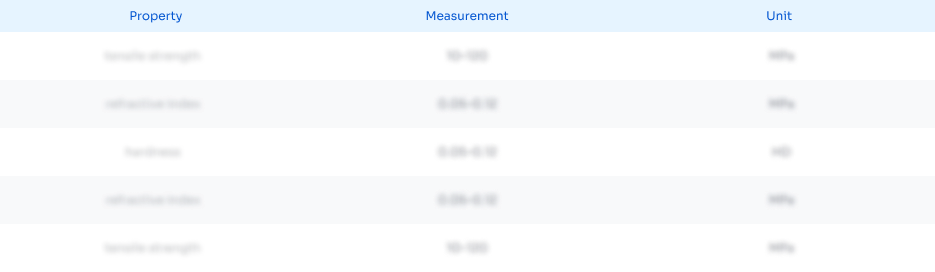
Abstract
Description
Claims
Application Information

- R&D Engineer
- R&D Manager
- IP Professional
- Industry Leading Data Capabilities
- Powerful AI technology
- Patent DNA Extraction
Browse by: Latest US Patents, China's latest patents, Technical Efficacy Thesaurus, Application Domain, Technology Topic, Popular Technical Reports.
© 2024 PatSnap. All rights reserved.Legal|Privacy policy|Modern Slavery Act Transparency Statement|Sitemap|About US| Contact US: help@patsnap.com