Preparation method of aqueous polyurethane emulsion and aqueous polyurethane emulsion prepared thereby
A water-based polyurethane and polyurethane fiber technology, which is applied in the directions of polyurea/polyurethane coatings, polyurea/polyurethane adhesives, adhesive types, etc., can solve the problems such as the preparation of water-based polyurethane emulsions by regeneration of polyurethane fibers.
- Summary
- Abstract
- Description
- Claims
- Application Information
AI Technical Summary
Problems solved by technology
Method used
Image
Examples
Embodiment 1
[0043] Example 1 A water-based polyurethane emulsion
[0044] The ratio of each raw material (unit: g) is as follows:
[0045]
[0046] Among them, the waste polyurethane fiber is waste polytetrahydrofuran diol type polyurethane fiber obtained by dry spinning with a soft segment ratio of 90%.
[0047] Prepared by the following steps:
[0048] 1. Clean and dry 60 g of the waste polyurethane fibers. spare.
[0049] 2. Put 100g of PTMEG, 0.05g of alcoholysis catalyst, 5g of BDO and 7g of DMBA into a four-hole round bottom flask, control the temperature at 95-120°C, fill with nitrogen and stir evenly, add 60g of clean and dry waste polyurethane fiber to the reaction In the bottle; heat preservation reaction for 2 hours, until the liquid is clear and the viscosity drops significantly to 1200-1500cPs / 90℃;
[0050] 3. When the temperature of the material drops below 50°C, put 50g of PTMEG, 4.5g of BDO, and 1.25g of TMP into the reaction bottle and stir evenly, then add 75g of T...
Embodiment 2
[0051] Example 2 A water-based polyurethane emulsion
[0052] Ratio of each raw material (unit: g)
[0053]
[0054] Among them, the waste polyurethane fiber is a waste polycarbonate diol type polyurethane fiber obtained by dry spinning with a soft segment ratio of 87%.
[0055] Prepared by the following steps:
[0056] 1. Clean and dry 50g of waste polyurethane fiber. spare.
[0057] 2. Put 120g of polyol PBA, 0.05g of alcoholysis catalyst, 6g of HDO, and 4.7g of DMBA into a four-hole round bottom flask, control the temperature at 95-120°C, fill with nitrogen and stir evenly, and put the cleaned and dried waste polyurethane Add 50g of fiber into the reaction bottle; keep it warm for 2 hours until the liquid is clear and the viscosity drops to 1200-1500cPs / 90°C.
[0058] 3. When the temperature of the material drops below 50°C, put the remaining polyol PBA45g, HDO4.5g and TMP1.25g into the reaction bottle and stir evenly, then add HDI72g, control the reaction at 70-75...
Embodiment 3
[0060] Example 3 A water-based polyurethane emulsion
[0061] Ratio of each raw material (unit: kg)
[0062]
[0063] Among them, the waste polyurethane fiber is a waste polycarbonate diol type polyurethane fiber obtained by dry spinning with a soft segment ratio of 90%.
[0064] Prepared by the following steps:
[0065] 1. Clean and dry 200kg of waste polyurethane fibers. spare.
[0066] 2. Put 75kg of PTMEG, 0.1kg of alcoholysis catalyst, 6kg of BDO, and 4.7g of DMPA into the reactor, control the temperature at 95-120°C, fill with nitrogen and stir evenly, and add 200kg of clean and dry waste polyurethane fiber to the reaction kettle. In the bottle; keep warm for 4 hours until the liquid is clear and the viscosity drops to 1200-1500cPs / 90℃.
[0067] 3. When the temperature of the material drops below 50°C, put the remaining PTMEG100kg and BDO19kg into the reaction bottle and stir evenly, then add 200kg of isophorone diisocyanate, control the reaction at 70-75°C for ...
PUM
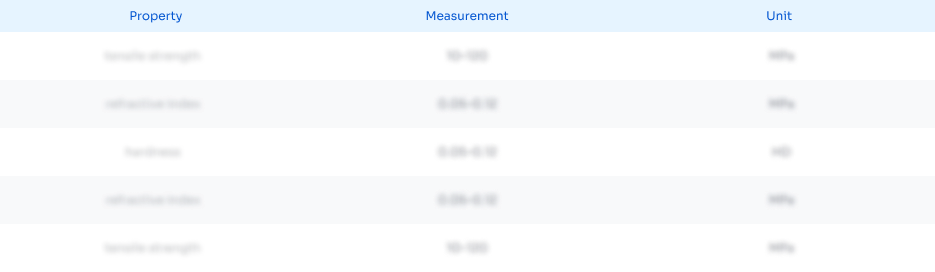
Abstract
Description
Claims
Application Information

- R&D Engineer
- R&D Manager
- IP Professional
- Industry Leading Data Capabilities
- Powerful AI technology
- Patent DNA Extraction
Browse by: Latest US Patents, China's latest patents, Technical Efficacy Thesaurus, Application Domain, Technology Topic, Popular Technical Reports.
© 2024 PatSnap. All rights reserved.Legal|Privacy policy|Modern Slavery Act Transparency Statement|Sitemap|About US| Contact US: help@patsnap.com