Defect mending method of palladium composite membrane
A defect repairing and composite membrane technology, applied in chemical instruments and methods, membrane technology, semi-permeable membrane separation, etc., can solve problems such as unrealistic, inapplicable, cumbersome operation, etc., and achieve the effect of convenient operation and low cost
- Summary
- Abstract
- Description
- Claims
- Application Information
AI Technical Summary
Problems solved by technology
Method used
Image
Examples
Embodiment 1
[0010] (1) Pd / Al sealed in the component 2 o 3 For the composite membrane, the flux and hydrogen permeation selectivity tests were carried out first. The test results are: at 350°C, the nitrogen flux is 0.086m 3 h -1 m -2 bar -1 , the hydrogen flux is 9.56m 3 h -1 m -2 bar -1 , the hydrogen-nitrogen selectivity is about 111.
[0011] (2) The component is placed in a high-temperature furnace, and the temperature is raised to 350°C by nitrogen purge.
[0012] (3) Put TEOS in a bubbler with the temperature controlled at 60°C and use N 2 Purge, control the purge rate to 20ml / min through the needle valve and rotameter, pass into the membrane side, another reaction gas O 2 Pass into the substrate side, the gas flow rate is 15ml / min.
[0013] (4) After reacting for 6 hours, the flux and selectivity test was carried out again. The result was: at 350°C, the nitrogen flux was 0.012m 3 h -1 m -2 bar -1 , the hydrogen flux is 7.98m 3 h -1 m -2 bar -1 , The hydrogen-nitr...
Embodiment 2
[0015] (1) Pd / Al sealed in the component 2 o 3 For the composite membrane, the flux and hydrogen permeation selectivity tests are carried out first. The test results are: at 350°C, the nitrogen flux is 0.056m 3 h -1 m -2 bar -1 , the hydrogen flux is 10.23m 3 h -1 m -2 bar -1 , the hydrogen-nitrogen selectivity is about 183.
[0016] (2) The assembly is placed in a high-temperature furnace, and the temperature is controlled at 330°C.
[0017] (3) Inject TEOS on the membrane side of the module with a syringe, and another reaction gas O 2 Pass into the substrate side, the gas flow rate is 15ml / min.
[0018] (4) After reacting for 4 hours, the flux and selectivity test was carried out. The result was: at 350°C, the nitrogen flux was 0.0096m 3 h -1 m -2 bar -1 , the hydrogen flux is 9.71m 3 h -1 m -2 bar -1 , the hydrogen-nitrogen selectivity is about 1012, and the selectivity is increased by nearly an order of magnitude.
Embodiment 3
[0020] (1) The palladium / stainless steel composite membrane sealed in the module is first tested for flux and hydrogen permeability selectivity. The test results are: at 350°C, the nitrogen flux is 0.097m 3 h -1 m -2 bar -1 , the hydrogen flux is 19.86m 3 h -1 m -2 bar -1 , the hydrogen-nitrogen selectivity is about 204.
[0021] (2) The components are placed in a high-temperature furnace, and the temperature is controlled at 400°C.
[0022] (3) Put TEOS in a bubbler with the temperature controlled at 80°C and use N 2 For purge, the purge rate is controlled at 20ml / min through the needle valve and rotameter, and it is passed into the membrane side, and another reaction gas is passed into the substrate side, and the gas flow rate is 20ml / min.
[0023] (4) After reacting for 6 hours, the flux and selectivity test was carried out again. The result was: at 350°C, the nitrogen flux was 0.016m 3 h -1 m -2 bar -1 , the hydrogen flux is 16.25m 3 h -1 m -2 bar -1 , the ...
PUM
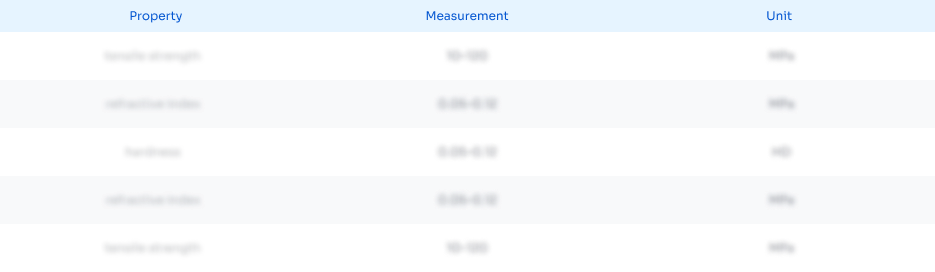
Abstract
Description
Claims
Application Information

- R&D
- Intellectual Property
- Life Sciences
- Materials
- Tech Scout
- Unparalleled Data Quality
- Higher Quality Content
- 60% Fewer Hallucinations
Browse by: Latest US Patents, China's latest patents, Technical Efficacy Thesaurus, Application Domain, Technology Topic, Popular Technical Reports.
© 2025 PatSnap. All rights reserved.Legal|Privacy policy|Modern Slavery Act Transparency Statement|Sitemap|About US| Contact US: help@patsnap.com