Square tapered aluminum alloy automobile front carling based on embedded carbon fiber
A technology of aluminum alloy and carbon fiber, which is applied to vehicle components, superstructures, bumpers, etc., can solve the problem of high energy absorption, low collision acceleration peak value, good crush mode, front longitudinal beam bending, and unsatisfactory collapse mode, etc. problem, to achieve the effect of low cost, simple assembly and good collision safety performance
- Summary
- Abstract
- Description
- Claims
- Application Information
AI Technical Summary
Problems solved by technology
Method used
Image
Examples
Embodiment Construction
[0015] The following description is merely exemplary in nature and not intended to limit the disclosure, application or use.
[0016] refer to Figure 4-6 , the structure of the patent square tapered aluminum alloy car front longitudinal beam has three parts: aluminum alloy outer wall 1, carbon fiber reinforced plate 2 and aluminum alloy tail plate 3. The assembly process is as follows: first produce the aluminum alloy outer wall 1, carbon fiber reinforced plate 2 and aluminum alloy tail plate 3, then install the carbon fiber reinforced plate 2 from the tail end of the aluminum alloy outer wall 1 formed into a square surround, and finally put the tail plate 3 Welded to the tail of the aluminum alloy outer wall 1, thereby completing the manufacture of the front longitudinal beam.
[0017] The following is the manufacturing process for the three parts:
[0018] The manufacturing process of the aluminum alloy outer wall 1: Since there are not many applications of aluminum alloy...
PUM
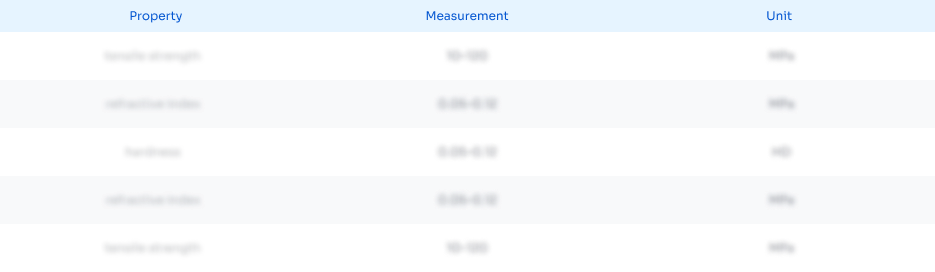
Abstract
Description
Claims
Application Information

- R&D
- Intellectual Property
- Life Sciences
- Materials
- Tech Scout
- Unparalleled Data Quality
- Higher Quality Content
- 60% Fewer Hallucinations
Browse by: Latest US Patents, China's latest patents, Technical Efficacy Thesaurus, Application Domain, Technology Topic, Popular Technical Reports.
© 2025 PatSnap. All rights reserved.Legal|Privacy policy|Modern Slavery Act Transparency Statement|Sitemap|About US| Contact US: help@patsnap.com