Sectional-type energy consumption brake circuit of permanent-magnet direct current motor
A DC motor and energy-consuming braking technology, which is applied in the direction of the reduction device of the DC motor, the electric motor/converter plug, etc., can solve the problems of braking torque drop, large braking torque, high potential, etc., and achieve fast braking speed , large braking torque and good effect
- Summary
- Abstract
- Description
- Claims
- Application Information
AI Technical Summary
Problems solved by technology
Method used
Image
Examples
Embodiment Construction
[0013] See attached figure 1 , the power supply is first sent to the voltage detection module, and the detection module detects two states of power on and power off. When the power is on, the control terminal outputs a low-level signal to lock all the braking modules behind, and the power passes through the diode D 0 Connect with the power supply terminal of the braking module in series at the back and finally supply power to the motor. At this time, all the braking modules are inactive and the motor is in normal working state.
[0014] When the power is turned off or the voltage drops to the motor stop voltage, the input detection module detects zero voltage or undervoltage status and confirms that the motor needs to stop, the control terminal of the input module turns to high level, canceling the locking of the following circuit, and the control The dynamic module starts to work.
[0015] The first energy consumption braking module starts to operate, the internal power tra...
PUM
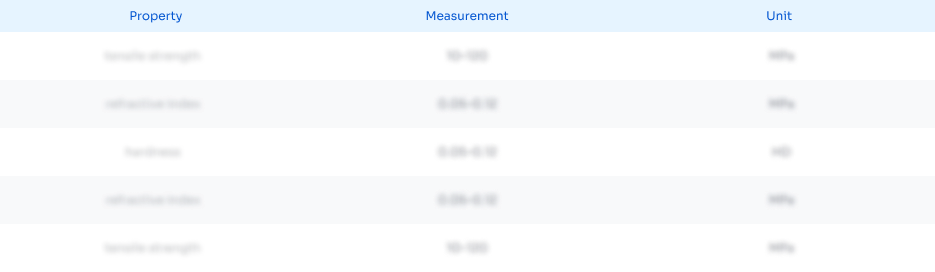
Abstract
Description
Claims
Application Information

- R&D
- Intellectual Property
- Life Sciences
- Materials
- Tech Scout
- Unparalleled Data Quality
- Higher Quality Content
- 60% Fewer Hallucinations
Browse by: Latest US Patents, China's latest patents, Technical Efficacy Thesaurus, Application Domain, Technology Topic, Popular Technical Reports.
© 2025 PatSnap. All rights reserved.Legal|Privacy policy|Modern Slavery Act Transparency Statement|Sitemap|About US| Contact US: help@patsnap.com