Method for preparing high-temperature composite coating on niobium-based surface by utilizing sol-gel method
A surface sol-gel, niobium-based alloy technology, used in coatings, metal material coating processes, solid-state chemical plating, etc., can solve the problems of coating cracks, different lattice structures, loss of protective matrix, etc. Improved bonding, easy handling, and reduced internal stress
- Summary
- Abstract
- Description
- Claims
- Application Information
AI Technical Summary
Problems solved by technology
Method used
Image
Examples
Embodiment 1
[0045]The method of preparing composite high-temperature coating by sol-gel method on niobium-based surface:
[0046] The first step: pretreatment of niobium-based alloy sample:
[0047] After pre-grinding, the niobium-based alloy samples were cleaned and degreased with absolute ethanol and acetone, and then dried by ultrasonic cleaning.
[0048] The second step: chemical treatment to prepare the intermediate bonding layer of the niobium-based alloy sample:
[0049] The steps of preparing the intermediate bonding layer are as follows:
[0050] 1. Chemical degreasing
[0051] The pretreated niobium-based alloy sample was treated with 15g / L Na 3 PO 4 12H 2 O, 10g / L Na 2 CO 3 and 5g / LNa 2 SiO 3 The formed mixed solution was soaked at a temperature of 50° C. for 4 minutes to obtain a niobium-based alloy sample after removing oil and impurities.
[0052] 2. Acid and alkali erosion
[0053] 1) The niobium-based alloy sample after degreasing and impurity removal was subjec...
Embodiment 2
[0070] The method of preparing composite high-temperature coating by sol-gel method on niobium-based surface:
[0071] The first step: pretreatment of niobium-based alloy sample:
[0072] After pre-grinding, the niobium-based alloy samples were cleaned and degreased with absolute ethanol and acetone, and then dried by ultrasonic cleaning.
[0073] The second step: chemical treatment to prepare the intermediate bonding layer of the niobium-based alloy sample:
[0074] The steps of preparing the intermediate bonding layer are as follows:
[0075] 1. Chemical degreasing
[0076] The pretreated niobium-based alloy sample was treated with 40g / L Na 3 PO 4 12H 2 O, 30g / L Na 2 CO 3 and 15g / L Na 2 SiO 3 The formed mixed solution was soaked at a temperature of 60° C. for 5 minutes to obtain a niobium-based alloy sample after removing oil and impurities.
[0077] 2. Acid and alkali erosion
[0078] 1) The niobium-based alloy sample after degreasing and impurity removal was sub...
PUM
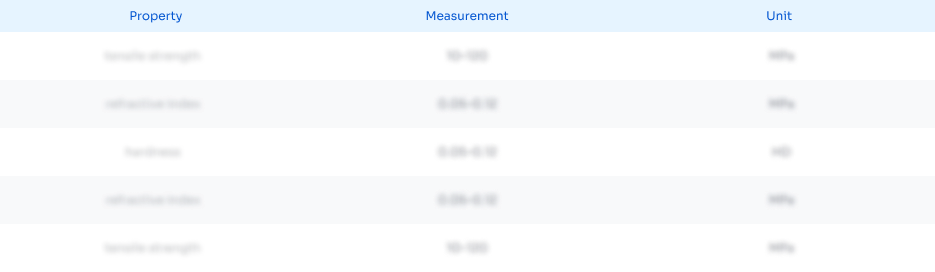
Abstract
Description
Claims
Application Information

- R&D
- Intellectual Property
- Life Sciences
- Materials
- Tech Scout
- Unparalleled Data Quality
- Higher Quality Content
- 60% Fewer Hallucinations
Browse by: Latest US Patents, China's latest patents, Technical Efficacy Thesaurus, Application Domain, Technology Topic, Popular Technical Reports.
© 2025 PatSnap. All rights reserved.Legal|Privacy policy|Modern Slavery Act Transparency Statement|Sitemap|About US| Contact US: help@patsnap.com