Turning jig device and manufacturing method dedicated to crankshaft
A fixture and crankshaft technology, applied in positioning devices, turning equipment, clamping devices, etc., can solve the problems of high technical level requirements, powerlessness, and investment of processors
- Summary
- Abstract
- Description
- Claims
- Application Information
AI Technical Summary
Problems solved by technology
Method used
Image
Examples
Embodiment Construction
[0029] The special turning fixture device for crankshaft, including left and right fixtures, is characterized in that the left and right fixtures are symmetrically installed on the left and right rotation centers of the lathe, and the structures of the left and right fixtures are basically the same, and each fixture is moved by the concrete and eccentric distance. And positioning mechanism, connecting rod neck index positioning and locking mechanism, crankshaft clamping mechanism, eccentric weight mechanism; the structure of each part is shown in the attached drawings as follows:
[0030] The main structure of the fixture see figure 1, the card specific 1 is used as the load-bearing body, which is characterized in that the left and right fixtures are symmetrically installed on the left and right rotation centers of the machine tool through the card specific 1, and one end can be the headstock, the other end can be the tailstock, or both the left and right are the headstock . ...
PUM
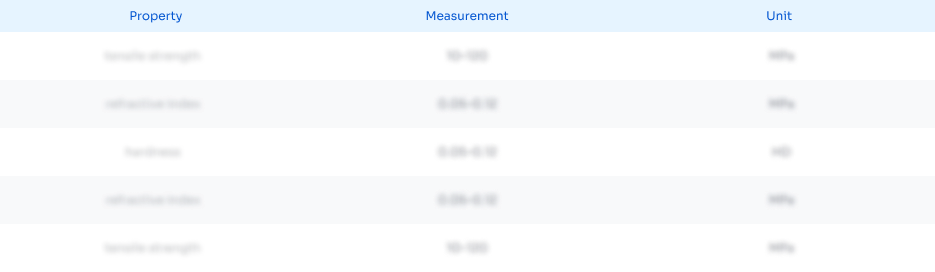
Abstract
Description
Claims
Application Information

- R&D
- Intellectual Property
- Life Sciences
- Materials
- Tech Scout
- Unparalleled Data Quality
- Higher Quality Content
- 60% Fewer Hallucinations
Browse by: Latest US Patents, China's latest patents, Technical Efficacy Thesaurus, Application Domain, Technology Topic, Popular Technical Reports.
© 2025 PatSnap. All rights reserved.Legal|Privacy policy|Modern Slavery Act Transparency Statement|Sitemap|About US| Contact US: help@patsnap.com