Flame-retardant fabric
A fabric and flame-retardant finishing technology, which is applied in the field of textiles and clothing, can solve the problems of unstable flame-retardant effect, reduced flame-retardant performance, and adverse effects on the human body, so as to avoid flames from harming the human body, reduce strength loss, and increase stability Effect
- Summary
- Abstract
- Description
- Claims
- Application Information
AI Technical Summary
Problems solved by technology
Method used
Examples
Embodiment 1
[0025] (1) Flame retardant finishing solution by padding: Dipping ordinary cloth with flame retardant finishing solution containing 400g / L THPS-U, 6g / L fatty alcohol polyoxyethylene ether and 20g / L high-concentration polyethylene, the rolling rate is greater than 70%~85%;
[0026] (2) Pre-drying: Pre-dry the fabric after step (1) padding the flame-retardant finishing solution in a drying oven at 90°C for 20 minutes;
[0027] (3) Ammonia fumigation: The fabric pre-dried in step (2) is subjected to ammonia fumigation treatment in an ammonia fumigation box, and the flow rate of ammonia fumigation is 1200L / min;
[0028] (4) Oxidation: Dip the ammonia-fumigated fabric in step (3) in an oxidizing solution with a concentration of 30%, and the rolling rate is 70%; the speed of dipping in the oxidizing solution is 30m / min, and place it for 2 minutes after dipping. Then wash in water, specifically water with a temperature of 35°C, and the washing time is 5 minutes;
[0029] (5) Drying...
Embodiment 2
[0031] (1) Padding flame retardant finishing solution: dip 100Kg pure cotton canvas into a flame retardant finishing solution containing 500g / L THPS-U, 5g / L fatty alcohol polyoxyethylene ether and 15g / L high-concentration polyethylene, the rolling rate 85%;
[0032] (2) Pre-drying: Pre-dry the fabric after step (1) padding with flame retardant finishing solution in a drying oven at 85°C for 15 minutes;
[0033] (3) Ammonia fumigation: The fabric pre-dried in step (2) is subjected to ammonia fumigation treatment in an ammonia fumigation box, and the flow rate of ammonia fumigation is 1300L / min;
[0034] (4) Oxidation: Dip the ammonia-fumigated fabric in step (3) in an oxidizing solution with a concentration of 35%, and the rolling rate is 75%; the speed of dipping in the oxidizing solution is 40m / min, and place it for 2.5 minutes after dipping , and then placed in water at a temperature of 35°C, and the washing time was 5 minutes;
[0035] (5) Drying: Dry the cloth washed in ...
Embodiment 3
[0038] (1) Padding flame retardant finishing solution: dip 100Kg pure cotton canvas into a flame retardant finishing solution containing 600g / L THPS-U, 4g / L fatty alcohol polyoxyethylene ether and 10g / L high-concentration polyethylene. The rate is 85%;
[0039] (2) Pre-drying: Pre-dry the fabric after step (1) padding the flame-retardant finishing solution in a drying oven at 80°C for 10 minutes;
[0040] (3) Ammonia fumigation: the fabric pre-dried in step (2) is subjected to ammonia fumigation treatment in an ammonia fumigation box, and the flow rate of ammonia fumigation is 1500L / min;
[0041] (4) Oxidation: Dip the ammonia-fumigated fabric in step (3) in an oxidizing solution with a concentration of 30%, and the rolling rate is 80%; the speed of dipping in the oxidizing solution is 35m / min, and place it for 2 minutes after dipping. Then put it in water at a temperature of 40°C, and wash with water for 5 minutes;
[0042] (5) Drying: Dry the cloth washed in step (4) in a ...
PUM
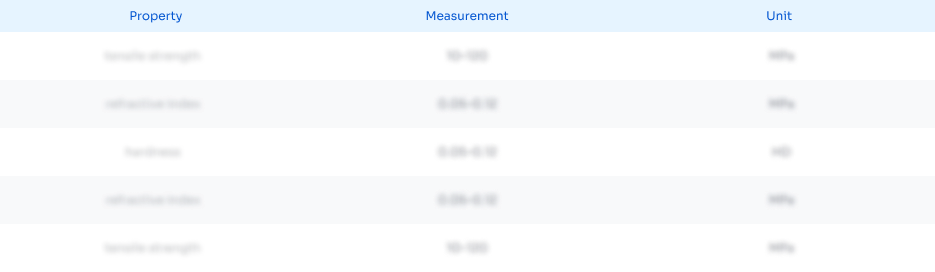
Abstract
Description
Claims
Application Information

- R&D
- Intellectual Property
- Life Sciences
- Materials
- Tech Scout
- Unparalleled Data Quality
- Higher Quality Content
- 60% Fewer Hallucinations
Browse by: Latest US Patents, China's latest patents, Technical Efficacy Thesaurus, Application Domain, Technology Topic, Popular Technical Reports.
© 2025 PatSnap. All rights reserved.Legal|Privacy policy|Modern Slavery Act Transparency Statement|Sitemap|About US| Contact US: help@patsnap.com