Dyeing process for chinlon bamboo joint fabric cotton fibre
A technology of cotton fiber and slub, which is applied in the field of dyeing technology, can solve the problems of many yarns and broken ends, high spinning speed and stretching ratio, and inability to obtain special effects, etc., so as to alleviate the shortage of water resources and power resources, Effect of shortening dyeing time and improving absorbency
- Summary
- Abstract
- Description
- Claims
- Application Information
AI Technical Summary
Problems solved by technology
Method used
Examples
Embodiment 1
[0012] The dyeing process of nylon slub cloth cotton fiber provided by the present invention includes the steps of pre-treatment, scouring, dyeing, drying and post-treatment of cotton fiber. The dyeing adopts reactive dyes, according to different color requirements and the ratio of various dyes , put the dye and sodium sulfate together into the chemical material of the dye vat for 20 minutes, then run it at room temperature for 10 minutes, heat up to the temperature required by the dye at a speed of 0.5-3°C / min, and choose the appropriate alkali according to the characteristics of different dyes Rate curve, use the automatic alkali adding equipment to start adding liquid alkali, after adding alkali, keep the temperature for 15 minutes, then remove the residual liquid, carry out post-processing, and prepare dyes according to the following ratio: Lanersol dye: 0~5% (owf.) , Novaclone dye: 0~5% (owf.); leveling agent 1~5g / L; Yuanming powder 15~45g / L; soda ash 5~15g / L.
[0013] Th...
Embodiment 2
[0017] The dyeing process of nylon slub cloth cotton fiber provided by the present invention includes the steps of pre-treatment, scouring, dyeing, drying and post-treatment of cotton fiber. The dyeing adopts reactive dyes, according to different color requirements and the ratio of various dyes , put the dye and sodium sulfate together into the chemical material of the dyeing vat for 25 minutes, then run it at room temperature for 20 minutes, heat up to the temperature required by the dye at a speed of 0.5-3°C / min, and choose the appropriate alkali according to the characteristics of different dyes Rate curve, use the automatic alkali adding equipment to start adding liquid alkali, after adding alkali, hold the temperature for 25 minutes, then remove the residual liquid, carry out post-processing, and prepare dyes according to the following ratio: Lanersol dye: 0~5% (owf.) , Novaclone dye: 0~5% (owf.); leveling agent 1~5g / L; Yuanming powder 15~45g / L; soda ash 5~15g / L.
[0018]...
Embodiment 3
[0022] The dyeing process of nylon slub cloth cotton fiber provided by the present invention includes the steps of pre-treatment, scouring, dyeing, drying and post-treatment of cotton fiber. The dyeing adopts reactive dyes, according to different color requirements and the ratio of various dyes , Put the dye and sodium sulfate together into the chemical material of the dyeing vat for 20-30 minutes, then run it at room temperature for 30 minutes, and raise the temperature to the temperature required by the dye at a speed of 0.5-3°C / min, and choose the appropriate one according to the characteristics of different dyes. Alkali-adding rate curve, use the automatic alkali-adding equipment to start adding liquid alkali, after adding alkali, keep the temperature for 30 minutes, then remove the residual liquid, carry out post-processing, and prepare dyes according to the following ratio: Lanersol dye: 0-5% (owf .), Noviclon dyes: 0-5% (owf.); Leveling agent 1-5g / L; Yuanming powder 15-4...
PUM
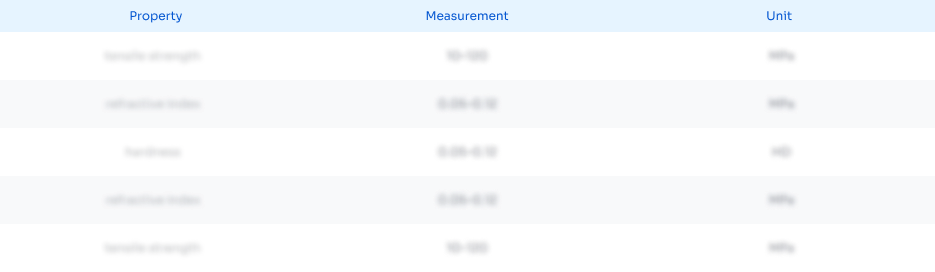
Abstract
Description
Claims
Application Information

- R&D Engineer
- R&D Manager
- IP Professional
- Industry Leading Data Capabilities
- Powerful AI technology
- Patent DNA Extraction
Browse by: Latest US Patents, China's latest patents, Technical Efficacy Thesaurus, Application Domain, Technology Topic, Popular Technical Reports.
© 2024 PatSnap. All rights reserved.Legal|Privacy policy|Modern Slavery Act Transparency Statement|Sitemap|About US| Contact US: help@patsnap.com